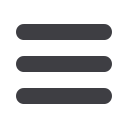

EuroWire – November 2007
59
Cutting &Welding
W
ire cutting is the very
model of a simple, straight-
forward operation. But it
has an extraordinary requirement
for precision, and always has had.
The highly mechanised, top-speed
wire cutter of 2007 can trace a
direct connection to the wire
shears that enjoyed pride of place
in the workshop of an artisan of
the middle industrial period. This
was a precision tool from its first
appearance.
The electronic servo feeder on a
modern cut-to-length line ensures
that precision to an extraordinary
degree, featuring a control with
display, speed potentiometer,
safety guard and powerful shock
absorbers. Guide rollers keep the
feedstock straight and perfectly
perpendicular to the cut. At the
same time, shearing knife clearances
can be preset – with a screw
adjustment – by hand.
Wire welding, too, was and is a
hands-on operation – even if,
these days, those hands are on
the keyboard of a console. A
renowned institute of welding
technology declares on its website:
“Necessity being the mother of
invention, we developed our own.”
Butt welding. Spot welding. Arc
welding. MIG. TIG. Stick. Orbital.
Each serves a special need; and,
impressive as it is, this partial list
will grow.Welding is an evolutionary
process if there ever was one.
Cutting and welding may serve the
obverse functions of separating
and joining, but they have this
in common: they began as bench
operations in the service of high
ideals of craftsmanship. And they
have never lost touch with their
origins.
feature
Meeting demand for high quality welds
August Strecker has recently increased its contacts in the fastener industry – adding
to its 75 years’ experience in providing buttwelding equipment to the wire and cable
industry. The increase is to meet the demand for a high performance reliable welder to
produce excellent weld quality at the feed of individual lines for manufacturing cold-
heading wire parts.
A typical machine for this process would be the Strecker type SS 120, working a range of
steel wires from 8-24mm in diameter. The welder is mounted on a platform that can be
moved into a working position close to the wire ends to be joined. This unit works with
two upset cycles to produce welds of high quality (the heat-affected liquid material is
almost completely pressed out of the joint), and incorporates an automatic de-burring
cycle producing flash-free joints of identical cross-section compared to the original
materials.
Another feature is that welding and, if necessary, annealing, can be done on the same
working height as often it is not possible to reposition the welded/de-burred wire into
annealing clamps on another level.
August Strecker GmbH & Co KG – Germany
Fax
: +49 5431 44221
:
strecker@strecker-limburg.deWebsite
:
www.strecker-limburg.deThe Strecker type SS 120
▲