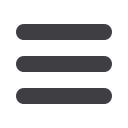

characterized by an exponential factor,
so only 37% of the units in a large
group will last as long as the MTBF
number; second, for a single supply,
the probability that it will last as long
as its MTBF rating is only 37%; and
third, there is a 37% confidence level
likelihood that it will last as long as
its MTBF rating. Additionally, half the
components in a group will have failed
after just 0.69 of the MTBF.
It should also be noted that this
formula and curve can be adapted to
calculate the reliability of a system:
Where A is the sum total of all
components failure rates ( A = 1n1 +
2n2 + … + ini)
Calculating the failure rate
Three methods can be used to
calculate failure rates, prediction
(during design), assessment (during
manufacturing) and observation
(during service life).
Prediction uses a standard database of
component failure rates and expected
Figure 1: The bathtub curve, failure rate plotted
against time with the three life-cycle phases: infant
mortality, useful life and wear-out.
Figure 2: Curve showing the probability that a
component is still operational over time.
life, typically MIL-HDBK-217 for
military and commercial applications
or Telcordia for telecom applications.
The MIL approach requires use of
many parameters for the different
components and includes voltage
and power stresses, while Telcordia
requires fewer component parameters
and can also take into account lab-
test results, burn-in data, and field-
test data. Finally, the MIL approach
yields MTBF data, while Telcordia
produces FIT numbers, (failures per
billion hours).
Using these databases and techniques
means several, often incorrect,
assumptions need to be made, such
as the assumption that the design is
perfect, the stresses are all known,
everything is operated within its
ratings, any single failure will cause
complete failure, and the database is
current and valid.
But, it is the least time consuming
method and by applying it consistently
across different designs, it can indicate
the relative reliability of topologies
and design approaches, rather than
absolute reliability.
Conversely, assessment is the most
accurate way of predicting failure
rate, but requires greater time and
resources. This method subjects
a suitable number of final units to
an accelerated life test at elevated
temperature, with carefully controlled
and increased stress factors.
One method, the HALT (highly
accelerated life test) approach, tests
a number of prototype units under
as many conditions as possible, with
cycling of temperature, input voltage,
output load, and other impacting
factors. HALT testing seeks to fatigue
a component, PCB, subassembly,
or finished product through either
intense stressing for fewer cycles, or
low level stressing for more cycles.
A second method, HASS (highly
accelerated stress screen) testing is
an accelerated reliability screening
technique used to reveal latent flaws
not detected by environmental stress
screening, burn-in, or other test
methods. HASS testing uses stresses
beyond initial specifications, but still
within the capability of the design as
determined by HALT.
New-Tech Magazine Europe l 45