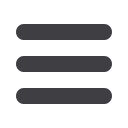

ROUND UP
ANALYTICAL INSTRUMENTATION
Loshini Govender,
manager of WearCheck’s
speciality laboratory.
Lab capacity boosted with new equipment
WearCheck
, Africa’s leading condition monitoring company, recently
invested over twomillion Rand on brand new cutting-edge laboratory
equipment. The shopping list included a new Gas Chromatograph
(GC), a new Inductively Coupled Plasma spectrometer (ICP) and a
new High Performance Liquid Chromatograph (HPLC). All the new
equipment uses top of the range technology to ensureWearCheck’s
legacy of accuracy and reliability of sample results and diagnoses.
While the company has already invested extensively in GC, ICP and
HPLC technology over many years – the laboratory capacity has
been significantly boosted with the addition of the latest testing
equipment.WearCheck serves the earthmoving, industrial, transport,
shipping, aircraft and electrical industries through the scientific analy-
sis of used oil from mechanical and electrical systems. Additional
services include the analysis of fuels, transformer oils, coolants,
greases and filters.The new laboratory equipment will benefit cus-
tomers across all industries, and particularly transformer analysis.
An expansive network now includes ten WearCheck laboratories
spanning the continent and beyond, including Gauteng, KwaZulu-
Natal, Mpumalanga Province, and international laboratories in
India, Dubai, Ghana, Mozambique and Zambia - at Lumwana mine
and Kitwe - with a presence in CapeTown, Rustenburg, Steelpoort,
Port Elizabeth, Zimbabwe and Namibia. ICP spectrometry analysis
provides high-speed detection and identification of trace elements at
very low concentrations in oil to determine the levels of wear metals,
contaminants and oil additives in lubricating oils.The ICP has been
installed inWearCheck’s Middelburg laboratory.
The HPLC separates compounds within a transformer oil sample,
revealing the presence and quantity of trace degradation products,
which in turn provides information on the operation of the transform-
er and whether there has been any breakdown of insulating material.
Enquiries:Tel. 031 700 5460 or email
support@wearcheck.co.zaTurnkey lubrication systems
for Kyrgyz gold mine
The
BMG Group
in conjunction with DRA Global successfully sup-
plied and installed a mill lubrication system including Motor Control
Centres (MCCs) and Programmable Logic Controllers (PLCs) for
the Ball Mill at Kumtor Gold Mine in Kyrgyzstan. Jan Grobler, BMG
National Product Manager: Instrumentation said: “Due to their ex-
tensive experience with mill control systems, system refurbishment
and with BMG lubrication systems in particular, DRA Global were
contracted to provide the MCCs and control solutions for the mills”.
One of the biggest challenges BMG faced for this project was the
altitude (4 000 masl) and ambient temperatures which can reach up
to −500 °C in winter.This required some unique design features to
enable the system to operate efficiently and reliably. “Most mining
operations established in the 1970s will soon be looking at equip-
ment upgrades, and we believe that the BMG Group is well posi-
tioned to become the preferred supplier of quality mill lubrication
systems in addition to our offering of professional technical support.”
Enquiries: Jan Grobler.Tel. 011 793 5562 or email
jang@bmgworld.netProtection of field-based
process instrumentation
A new high capacity, easy-access enclosure from Intertec provides
plant engineers with a versatile alternative to free-standing cabinets
for the environmental protection of field-based process instrumenta-
tion. Developed at the request of a Russian oil refinery, the enclosures
are made from tough glass reinforced polyester (GRP) and include
highly insulated options for use in extremely cold climates. They
also offer more space than typical instrument enclosures, to allow
plant personnel to use gloved hands when accessing the equipment.
Typical applications include housing differential pressure flowmeters
and process transmitters in refineries, petrochemical and chemical
processing plants.The new enclosures are the latest addition to In-
tertec’s Diabox range of instrumentation protection solutions, which
are moulded two-part enclosures that open diagonally to provide
easy access for operating and maintenance staff. The new Diabox
277 enclosure measures 600 x 750 x 600 mm (H xW x D) and has an
internal volume of approximately 277 litres, depending on the level
of insulation specified. Manufactured from a high-performance grade
of GRP using a hot-press moulding process, the standard versions
of the enclosure provide an exceptionally robust and rigid housing;
they have a wall thickness of 6 mm yet typically only weigh 18 kg.
The latest addition means that Intertec’s Diabox range of enclosures
now includes six models, with capacities ranging from 27 up to 277
litres, enabling plant designers to choose the optimum size for their
application – for single or multiple process instruments.
Enquiries:Visit www.intertec.info9
May ‘15
Electricity+Control