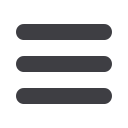

GOLD
August 2016
MODERN MINING
31
The process flowsheet at Brakpan
With the FFG now fully operational for well over a year, all the slurry enter-
ing the Brakpan plant enters the flotation section after passing over linear
screens to remove organic material and debris. After the material is condi-
tioned with reagents, it enters the float cells where it is separated into two
streams. One stream, the flotation concentrate, contains the sulphides while
the second stream, the flotation tails, is made up of lower-grade material
which is treated in the Brakpan plant’s main CIL circuit.
The concentrate stream is subjected to the new fine-grind process,
which involves milling the slurry material with tiny beads using four verti-
cal stirred mills (sourced from FLSmidth). At this stage the milled product
has been liberated from the sulphides, making recovery of the previously
encapsulated gold easier as it comes into contact with cyanide during the
leaching process that follows.
The dissolved gold is adsorbed onto activated carbon and the ‘loaded
carbon’ in each circuit enters the carbon treatment section where the gold
is eluted from the carbon. The carbon then returns to the CIL circuit via a
regeneration kiln. Once the gold has been eluted, it undergoes electro-win-
ning where the gold is precipitated, calcined and smelted in the existing
smelthouse.
DRDGOLD’s infrastructure
extends over a 62 km long
portion of the central and
east Witwatersrand.
a record gold production in March last year.
“Getting the FFG circuit right was a difficult
task, as we were dealing with so many variables
that it was difficult to pinpoint exactly why we
weren’t getting the recoveries we expected,”
Schoeman told
Modern Mining
. “We were fairly
certain that the basic design was sound but
we identified over 50 enhancements that we
thought could make a difference and system-
atically implemented them all. Then we started
up the FFG circuit in stages, making sure that
each float stream was stable and achieving the
desired parameters before we moved onto the
next one.”
The enhancements included changes to the
carbon management circuit, increasing the
water storage capacity and management within
the plant, modifications to control systems and
ensuring increased tailings thickener availabil-
ity prior to the low grade CIL circuit.
Although the FFG circuit is now working
well, Schoeman said that DRDGOLD is con-
stantly looking at ways to improve its operation.
“We believe we can get even better numbers out
of the FFG. For example, we currently have a
mill feed of about 80 % passing 35 microns and
we mill that down to 80 % passing 24 microns.
The optimum is to go down to 20 microns but
there is a cost offset. We will get there – it’s a
continuous optimisation exercise.”
Looking ahead, Schoeman said that Ergo’s
total treatment capacity was now 2,4 Mt/
month, with the Brakpan plant (after the recent
refurbishment of five CIL tanks) now hav-
ing the ability to process 2,1 Mt/month and
the Knights facility a further 300 000 tonnes/
month. “The current restraint on our pro-
duction is not plant capacity but deposition
capacity – specifically the rate at which we can
safely deposit material at our Brakpan Tailings
Deposition Facility (TDF) – and if we want to
go to the 2,4 Mt/month level, then we need to
address this issue,” he explained.
“The way we intend to do this is to make
use of the Withok site which is immediately
adjacent to the Brakpan TDF. Earlier this
year we received the necessary regulatory
approval to incorporate the Withok footprint
into the TDF and, once implemented, this
will increase Ergo’s deposition capacity from
200 Mt to approximately 800 Mt – enough to
receive most of the mine tailings in and around
the Johannesburg area and to assure Ergo’s life
of mine for at least another 25 years. When
exactly we implement the project is dependent
on a feasibility study which is currently well
advanced and which is looking at all aspects
of the Ergo operation,” he concluded.
Photos (unless otherwise acknowledged) courtesy
of DRDGOLD