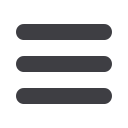

PRODUCT News
August 2016
MODERN MINING
69
The Counter Current Decantation (CCD)
thickener circuit at Swakop Uranium’s
Husab project demonstrates the potential
of an FLSmidth package solution. Designed
and supplied by FLSmidth, this CCD circuit
has the largest diameter thickeners of their
kind to be installed on the African conti-
nent in this type of application.
Located near Swakopmund on the west
coast of Namibia, Husab will reportedly be
the largest open-pit uranium mine in the
world, and will mine 150 million tonnes of
rock per year and produce over 15 million
pounds of uranium oxide.
The shareholders of Swakop Uranium
are the Republic of Namibia, through state-
owned mining company Epangelo, and
the People’s Republic of China, through
state-owned CGNPC.
The scope of the FLSmidth order for
the Husab CCD circuit comprises eight
40 m diameter thickeners. One is a high
density pre-leach feed thickener and the
other seven are high rate CCD thickeners.
FLSmidth is also supplying a 25 m diam-
eter ADU (ammonium diuranate) high rate
thickener for installation further down
the process. In addition to this, 38 Krebs®
centrifugal pumps will also be installed
in all slurry pumping applications on the
project.
Describing a CCD thickener circuit,
Terence Osborn, Sales & Market Manager,
Base and Precious Metal for sub-Saharan
Africa at FLSmidth, says the technology is
used to recover soluble metal as pregnant
liquor solution from ore leach residue.
The basis of CCD operation is to con-
centrate the leached solids, thereby
minimising liquor content in the under-
flow slurry that flows in one direction. The
underflow slurry is then diluted with wash
liquor that flows in the opposite direction,
while the leached solids are concentrated
repeatedly. The amount of liquor in the
thickener underflow contributes to deter-
mining the number of CCD stages required
to recover the desired amount of soluble
metal.
The nature of the process means that
pumps are integral to the CCD circuit as
these transfer the solution and the slurry
from one stage to the next. Slurry being
transferred has a very high density which
maximises the wash efficiency mak-
ing this type of application specifically
FLSmidth provides package solution for Husab
suited to Krebs® pumping technology.
“The Krebs® pumps are well matched
from a process performance perspective
and the ideal pump for the transfer of
material between the stages within the
CCD circuit. Centrifugal pumps are capable
of achieving the high flow rates required in
this application and the Krebs® pump has
the added benefit of its patented wear ring
design which minimises wear enhancing
pump performance and life,”Osborn says.
It is significant that Krebs® pumps were
FLSmidth 40 m diameter CCD thickeners installed for Swakop Uranium.
selected for the transfer of slurry from the
underflow. The majority of pumps installed
are Krebs® slurryMax™ units with a smaller
number of Krebs® millMAX™ pumps being
used.
The tailings pumps, also supplied by
FLSmidth, have been installed in series.
These Krebs® slurryMAX™ pumps will
facilitate the transfer of material over the
extended distance from the process plant
to the tailings storage facility.
Terence Osborn, FLSmidth, tel (+27 10) 210-4820
Innovative prototype fan to be installed at Mponeng
Local fans and ventilation firmMechCaL has
been appointed by AngloGold Ashanti to
install a vapour compressor fan prototype
at Mponeng mine.
The fan will be installed as part of a
vapour compressor which is an integral part
of a vapour compression refrigeration plant
at Mponeng. The fan in question will form a
flexible blade compressor that leverages the
outstanding strength of high end composite
materials. The prototype has been in devel-
opment since 2012. Refrigeration plants
are generally required in deep level min-
ing where underground rock temperatures
exceed the legal limits and the air needs to
be cooled down to acceptable working envi-
ronment levels.
According to Michael Minges, Director of
Operations at MechCaL, the use of carbon
composites allows the product to be used
in extreme operating conditions of high
loads. The fan is also suited to applications in
refrigeration plants and desalination plants.
MechCaL’s patented designs are coupled
with the use of light weight composite
materials to create fans that boast increased
efficiency, operational and energy savings,
and lower mean time between failures.
“The use of composites in these systems
is a niche application and use of such mate-
rials allows us to re-engineer the vapour
compressor and blades that can with-
stand the highly loaded application where
each blade experiences loads of up to 70
tonnes,” says Minges. “These are mainly due
to centrifugal loading, as the fan of 2,4 m
outer diameter spins at levels of close to
3 500 rpm.
“Some tricky design issues needed to be
addressed with innovative and well-engi-
neered solutions that address issues such
as the blade tip speed crossing the sound
barrier at 400 m/s at 120 deg C and reach-
ing speeds of 440 m/s. It is also critical to
ensure that during the operational running
of the fan the natural modes of the structure
do not get excited – which makes the stiff-
ness design of the fan blade material layup
of vital importance.”
MechCaL, website:
www.mechcal.co.za