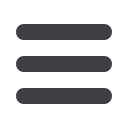

Feature
Springs
September 2012
48
www.read-eurowire.com“
ACID-FREE
PROCESS FOR STEEL
ROD CLEANING & SURFACE
PREPARATION”
“New Way to Draw Steel Wire
in the 21
st
Century”
DCCD process features:
• Eliminates acid, borax and precoatings
• Zero energy consumption
• Direct drawing from bare rod with no
speed limitation, for H/C and L/C
• New Lubricant Viscosity Control
provides exceptionally adherent coating
• Adjustable lubricant residual
• Zero lubricant waste
• Recommended for severe drawing
applications (spring, rope, bead,
CO
2
welding, PC strand, plating quality)
• H/C wire drawn at 18 m/s (3600 ft/min)
• Up to 8 times longer die life
• Exiting wire temp. 45°C (113°F)
• Greatly improved wire ductility
DECALUB
31, avenue de Condé
77500 CHELLES, FRANCE
Fax: +33 1 60 20 20 21
E-mail:
info@decalub.comWebsite:
www.decalub.comNew dosing unit for all free flowing plastic
The new Plasticolor 1500 Dosing Unit is suitable for the handling of all free flowing
plastic material, such as powder, fine or coarse granules, reground, flakes or
agglomerate. With an output range of 0.1–35kg/h the new Plasticolor 1500 is the right
choice for the dosing/blending of all additives such as masterbatch, UV-stabilisers,
fillers, kickers, etc. In the case of very small extruders and injection moulding machines
with a capacity of up to 30kg/h the new Plasticolor 1500 could also be used as the main
material dosing unit in mixing stations.
With the Plasticolor 1500 the handling has been improved and time consumption
for material change and cleaning of the unit can be reduced considerably. The main
highlights on the new Plasticolor 1500 are:
• Newly designed round flow channels in the material inlet and the dosing cylinder
resulting in more precise and constant dosing
• The quick discharge with a diameter of 60mm can be easily operated and allows
very quick material changeover, for better and cleaner discharge of material, a
flexible hose can be mounted
• Based on the completely round flow channels – without any corners, steps or
undercuts – it is possible to clean the unit extremely quickly and easily
• The sealing at the screw shaft meets the highest requirements in respect to
closeness of the unit and cleanness in the surrounding
• The integrated neckpiece slide (for the closing of the material flow into the
production machine and simultaneous diversion of the material flow into the test
opening) now has a larger round material outlet. Also here, a flexible hose could
be connected. This larger round outlet also allows the handling of more coarse
materials without any problems
• In order to protect motor and/or gearbox a backpressure protection is integrated in
the new Plasticolor 1500
Various available options complete the Plasticolor 1500:
• Both the quick discharge and the neckpiece slide can be upgraded for pneumatic
operation. This shortens and simplifies the handling
• For extreme fine powders an additional shaft seal can be installed. Between the
outlet of the storage hopper and the material inlet of the Plasticolor 1500 dosing
unit a sensor adaptation plate can be mounted
• The new Plasticolor 1500 dosing unit can be upgraded with an additional screw
detection, which works in conjunction with the PPM II Control. Thus wrong dosing
results are avoided
• For special applications the Plasticolor 1500 could also be supplied without the
neckpiece slide.
Woywod Kunststoffmaschinen GmbH & Co Vertriebs-KG – Germany
Website
:
www.plasticolor.de▼
▼
The new Plasticolor 1500 fromWoywod