
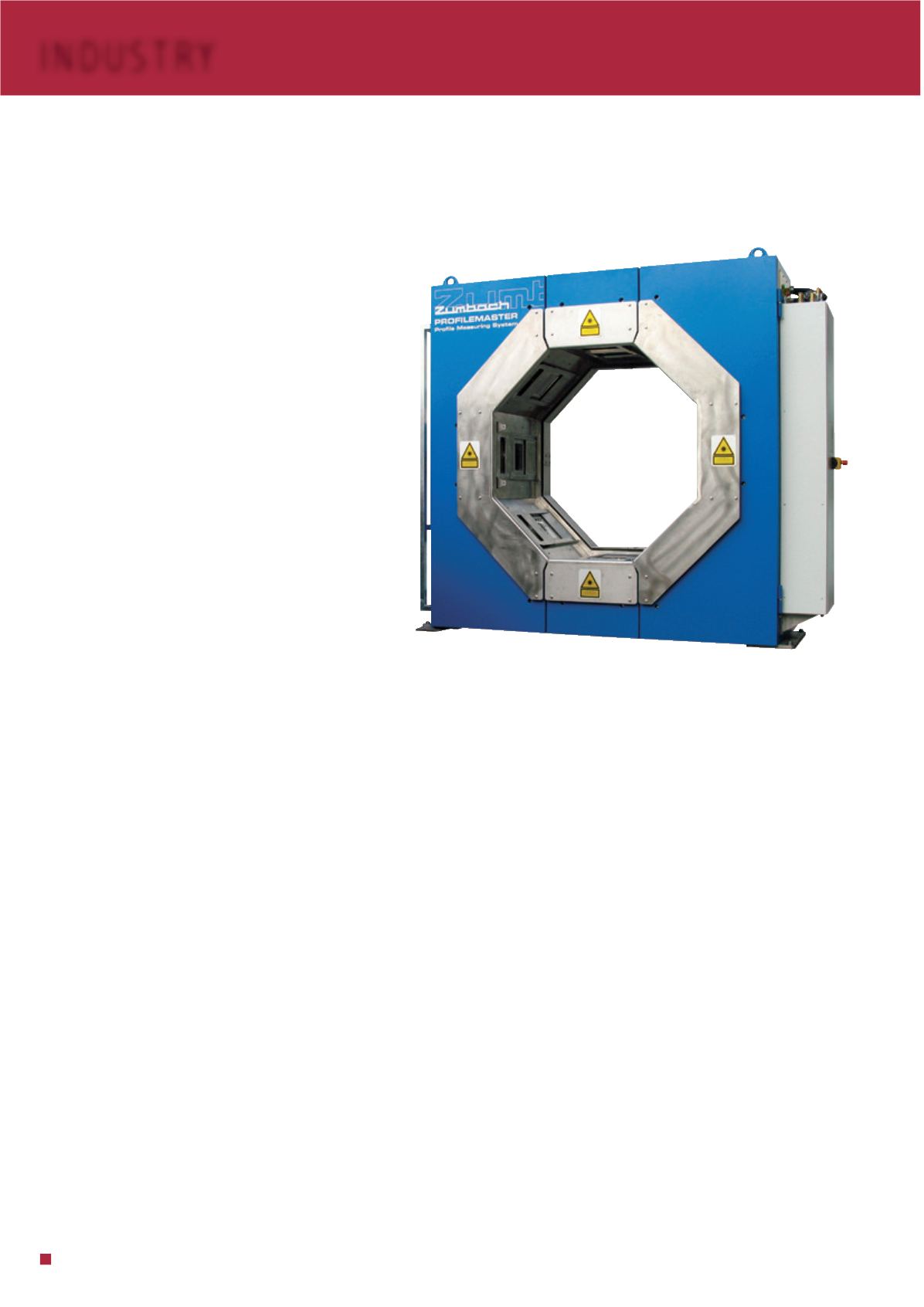
6
J
uly
2016
I NDUS T RY
Zumbach equips German hot rolling mill
with profile measuring system
ZUMBACH
Electronic,
based
in Switzerland, recently sold a
Profilemaster
®
SPS 800-S8 profile
measuring system to Germany-based
Hoesch Schwerter Profile GmbH.
Hoesch is part of the Italian Calvi
Holding group and produces various
steel profiles on its hot rolling mill. The
company is amanufacturer of customised
special profiles made of steel. These are
used in virtually all areas of the steel
processing industries.
Zumbach is a supplier of non-contact
measurement solutions for the steel
industry as well as other industries such
as wire and cable, plastics and rubber.
Hoesch’s partnership with Zumbach
shows trust in its extensive experience
in the field of non-contact measurement
technology and allows it to make a leap
forward in manufacturing capability,
benefiting from the latest in technological
advantages.
For Zumbach, Hoesch is an ideal
partner because the company focuses
on quality, precision and close customer
relationships – virtues that Zumbach
also admires.
In order to reach the increasing
demands of accuracy and reliability
of steel profiles and to increase the
efficiency of the hot rolling mill, Hoesch
decided to acquire a Profilemaster
®
SPS 800-S8 system. Thanks to this
measuring system, Hoesch will have a
more competitive position in the market.
Among other benefits, start-up and
changeover times can be extensively
reduced.
Some of the main advantages are:
eight cameras which can be equipped
modularly, any shape can be captured
and measured; up to 16,000 points/
contour (2,048/camera) = 5,734,400
points/second; high sampling rate of
350-500/second (full profiles/second);
four different colours of laser = no
interference; easy and quick calibration
check (can be done by the customer
within few a few minutes); and real-time
monitoring of complex profiles.
Zumbach Electronic AG
– Switzerland
Email:
sales@zumbach.chWebsite:
www.zumbach.comBarnshaws helps visitors into Orbit
ONE of the defining structures of the
London 2012 Olympics, theArcelorMittal
Orbit, reaches 115m into the London
skyline around Queen Elizabeth Olympic
Park. Designed by Sir Anish Kapoor and
Cecil Balmond, the landmark is now
incorporating a 584ft-long helter-skelter
to provide visitors with a unique view of
the capital.
Set to be the world’s largest tunnel
slide, riders will be able to reach the
heights of the structure thanks to the
metal bending expertise of Barnshaws
Section Benders’ Scottish division.
When the structure was erected in
2012, Barnshaws’ Hamilton branch
was contracted to help produce the
complex staircase to provide visitors
with access to the top of the freeform
skeletal structure. Due to the design
peculiarities of the sculpture, the
staircase required numerous sections
of varying lengths and curves to
achieve the desired effect.
Due to the great variance of sections
required to fabricate the staircase,
months of testing time was needed to
guarantee the correct specification of
section, and that the spiralling applied
to the sections was accurate. Each
section was required to be mandrel
spiralled – a new process developed
by Barnshaws – with each particular
section displaying varying length and
spiral attributes. Every piece of each
particular module had to be of the
highest quality.
The structure was initially opened as
a centrepiece attraction for the London
2012 Olympic Games, before being
closed for its redevelopment into a
public space, reopening to the public in
April 2014.
Barnshaw Section Benders Ltd
– UK
Fax: +44 121 557 5323
Email:
info@barnshaws.comWebsite:
www.barnshaws.comProfilemaster
®
SPS 800-S8