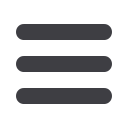

Since its introduction in the 1800s, welding has proved itself to every generation
of pipe makers by meeting the needs of the new day. In 2016 that means
smooth incorporation into the automated mechanised or robotic processes that
yield products whose very names invoke demanding, specialised applications:
high-temperature steam pipe; high-pressure pipe for deepwater oil well
projects; high-purity pipe for the food and beverage industries.
A pipe weld today is as sensitive as ever to the effects of heat and no less
vulnerable to distortion; it still calls for skilled workmanship if it is to be
smooth, uniform and sound: not too wide, not too high. But current standards
of productivity also mean that welding is a station in a multi-activity system
whose efficiency depends on perfect coordination with upstream and
downstream processes that themselves operate at top speed and with no
allowance for glitches.
It is a challenge that is met daily – and handily – in a state-of-the-art pipe mill.
Pipe welding
Photo: Kjellberg Vertrieb GmbH, Germany