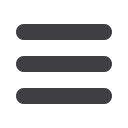

EuroWire – January 2008
46
english technology news
SonobondUltrasonics’splicing technology
has significantly reduced production time
for a major manufacturer of automotive
wire harnesses.
This is based on information received from
Curt Reynolds, director of manufacturing,
at J&M Products in San Fernando,
California, USA. Reynolds reports that
his company has cut splicing time by a
dramatic 60% since installing Sonobond’s
SpliceRite™ ultrasonic wire splicers.
Prior to introducing Sonobond’s ultrasonic
splicing technology into its production
process, J&M Products used a two-stage
system of mechanical banding and
soldering.
The Sonobond SpliceRite™ ultrasonic wire
splicer offered J&M the practical, cost-
effective solution it needed for faster,
more reliable wiring harness assembly.
The company’s research showed that this
proven ultrasonic technology quickly
splices wire bundles and creates a true
metallurgical bond – without producing
arcs, sparks, or fumes.
J&M Products also liked the fact that this
Sonobond system eliminates any need to
crimp, clip, solder, or dip in order to make
strong, high-quality wire connections.
And, unlike other ultrasonic welders, the
SpliceRite™ is able to bond wire bundles
even if the wires are oxidised or tin plated.
The SpliceRite™ comes in both 1,500
and 2,500 watt capacity and utilises
Sonobond’s patented‘wedge-reed’system
of high vibratory force and low amplitude
coupling. Welds can be controlled
by height, energy or time. The unit’s
microprocessor is able to interface with a
computer via an RS232 port.
Sonobond Ultrasonics Inc – USA
Fax
: +1 610 692 0674
:
info@sonobondultrasonics.comWebsite
:
www.sonobondultrasonics.comReduced production time from Sonobond
▲
Drop in splicing time using Sonobond technology
Design and selection of
bows for bunching and
stranding machines offer
a variety of challenges to
users and manufacturers.
Despite a relatively simple
basic design concept
and limited number of
components, applicable
materials and shapes
allow for a multitude of
combinations.
As a supplier of quality
spare parts, WireTrex not
only provides standard
bow models specified by machine manufacturers but also numerous variations.
The company offers a wide variety of ceramic and carbide bow guides as well as
wear strips.
In addition, WireTrex is prepared to assist customers to find the right combination
for their individual applications and help develop innovative solutions where
needed.
WireTrex Ltd – Germany
Fax
: +49 201922 9329
:
info@wiretrex.comWebsite
:
www.wiretrex.comHelp at hand fromWireTrex
A selection of bows fromWireTrex
▲