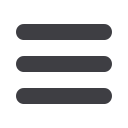

ROUND UP
Launch of locally manufactured globe valve
Mitech ControlValves has launched a locally designed and manufac-
tured High Pressure Globe StopValve. High-pressure stop valves are
used in the most extreme high pressure and temperature applica-
tions. Eskom remains one of the largest consumers of these valve
types, with thousands of units required in power plants across the
country. Up until now, there has been no local manufacturing capa-
bility to produce the valves required to specification. With no local
capability available, cost for the purchase and maintenance of these
valves remains high. In answer to this challenge,
Mitech
has been
working in close consultation with Eskom over the last two years, to
conceptualise, design and locally manufacture a high pressure stop
globe valve that will fulfil the technical and safety requirements as
well as the local content requirements as set out inThe Department
ofTrade and Industry’s (the dti) designation Instruction Note for the
procurement of valves and actuators.
General Manager for Mitech, Pieter Badenhorst highlights the
degree to which the unit is locally produced stating that “although
we have to import some of the material used in the manufacturing
process such as bar-stock which is not produced in the country at
present the valve remains 80 - 90% locally manufactured.” Using
Mitech’s design, locally sourced materials, local castings, machin-
ing, assembly and testing, the valve conforms to all the criteria for
local content.
Badenhorst explains that it would be very difficult to simulate the
extreme conditions that would be required to test their valve in the
laboratory, and therefore, Eskom has agreed to install the valves at
appropriate test sites for a trial period at their power plants, to fully
evaluate the valve’s performance. Mitech has committed to provid-
ing technicians working on Eskom’s plants with training as well as
a full service manual to ensure effective incorporation of the valve
into the power plants.
The whole unit comprises 33 components, most of which are easy
to maintain. The body of the valve is a one-piece investment cast
design, eliminating threaded or bolted pressure retaining parts.The
unit has a fully replaceable seat, which can be extracted while the
valve remains welded into the line.
Enquiries: Pieter Badenhorst.Tel. +27 (0) 11 657 6000 or
PRESSURE + LEVEL MEASUREMENT
New precision digital pressure gauge – enhanced performance spectrum
Extended measuring ranges, large data log-
ger, wireless functionality and streamlined
menu operation: With the model CPG1500,
WIKA
has launched an improved precision
digital pressure gauge with an appealing
price/performance ratio.The new calibration
and test instrument has been designed for
versatile use. The CPG1500 covers pressure
ranges up to 0 ... 1,000 bar andmeasures with
an accuracy of up to 0,05% of span. Its data
logger can record up to 50 measured values
per second.The data is transmittedwirelessly
and can be processed using theWIKACal soft-
ware. Further functionality, such as min/max
memory or integrated temperaturemeasure-
ment, enhances the performance range.The
newmenu structure of the CPG1500 enables
a quicker intuitive input for all parameters. A
5½-digit display with bargraph and a large
text field supports the analysis of measuring
points on site. The measuring quality of the
CPG1500 is ‘packaged’ within a robust design.
As an intrinsically safe instrument (IECEx,
ATEX, CSA approvals) and with IP65 ingress
protection, it offers reliability and durability,
even with extreme process conditions.
Enquiries:WIKA Instruments.
Tel. +27 (0) 11 621 0000 or
Mitech’s Pieter Badenhorst.
Electricity+Control
June ‘16
14