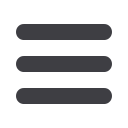

S
eptember
2008
www.read-tpt.com168
›
T
ube
B
ending &
E
ndforming
T
echnology
The machine offers very high working
speeds, with a bending speed of 120°/sec,
rotation speed of 240°/sec and feeding
speed of 908mm/sec.
Langbow Ltd is the supplier of Soco
bending machines for the UK market.
Soco Machinery Ltd
– Taiwan
Fax
: +886 4 23592386
:
socomc@seed.net.twWebsite
:
www.socomachinery.comLangbow Limited
– UK
Fax
: +44 1889 578 872
:
sales@langbow.co.ukWebsite
:
www.langbow.co.ukbending, rotation, feeding/material booster
servo power, pressure die assist, pressure
die mobility (up/down), pressure die
clamping, and mandrel mobility (forward/
backward).
The machine also has a clamping die,
machine head seat horizontal mobility,
carriage seat vertical mobility (up/down),
tail seat vertical mobility (up/down), and
pipe support vertical mobility (up/down).
A clutch feeding system is fitted for both
high and low boosting speeds in the same
machine. A servo controlled pressure die
vertical movement allows only 1 pressure
die for all bending stacks.
Other features include different bending
parts from the same tube, recapture
function and boosting shot for the last
bend.
Soco, Taiwan, has launched its latest all
electric 12-axis mandrel tube bending
machine. Branded the SB-80x12A–MR–
PT+2C, the machine includes a boost
bending facility for 1D bending and
minimum wall thinning.
The machine has multi-stacks and multi-
radius, while DBS cutoff shearing (double
blade shearing) is also offered to speed up
production of many parts from a single tube
length.
The highest efficiency-DGT (direct gear
transmission) machine is ideal for the high
volume producer particularly in the field
of exhausts and manifolds for automotive
applications.
The SB-80x12A–MR–PT+2C offers superior
performance and can achieve a number
of operations. These operations include
Soco’s SB-80x12A–MR–PT+2C mandrel tube bending machine is available with 12-axis
All electric 12-axis mandrel tube-bending machine
The machine has a boost bending facility for 1D
bending
The bend head is mounted on a gantry
structure spanning the support table, while
a fully automatic 3-axis support table
moves beneath the bending head carrying
the product whilst it is being manufactured.
The finished product is transported to the
edge of the machine for unloading, and
an automatic unloading mechanism is
available to sweep the finished parts from
the automatic table to a receiving bench or
conveyor system.
The
programming
software
offers
engineering units as the programming
medium, with repeat facilities to reduce the
size of programs for regular shaped parts.
The table movements are automatically
calculated from the component program.
Pneuform Machines Limited
– UK
Fax
: +44 1420 87003
:
pneuform@pneuform.comWebsite
:
www.pneuform.comPB600 solar/serpentine bender is based
on the traditional Pneuform design for
straightening and feeding, and can produce
parts up to 6m square.
A new bend head
has been introduced
that encloses the
tube
during
the
bending movement,
to produce improved
bend quality.
The bend head has
two rollers and a
shift mechanism to
allow the centre of
the rotation to be set
around either roller,
enabling bending in
both directions.
Pneuform Machines Ltd, UK, has extended
its range of bending machines to meet
the requirements of the solar technology
and heated/cooled panel industries. The
The PB600 solar/serpentine bender is designed for the requirements of solar
technology
Range of benders for solar technology industry