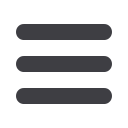

171
S
eptember
2008
www.read-tpt.com›
T
ube
B
ending &
E
ndforming
T
echnology
AddisonMckee has launched a highly
advanced mandrel force monitor designed
to improve finished component quality when
working with the company’s tube bending
machines. The advanced monitoring
process is able to highlight even small
variations in mandrel performance.
“Typically, the problem with mandrel
failure sensor systems,”
comments
AddisonMckee’s
director
of
global
marketing, Mr Christian Rogiers,
“is that,
while being effective, they can lead to
increased maintenance and machine
downtime caused through non-relevant
warnings. We have, consequently, been
reluctant to embrace such solutions.”
“Following the signing of an agreement with
process monitoring devices company, OES
Inc of Canada,”
he added,
“I am delighted
to announce that AddisonMckee is now able
to offer a highly advanced, robust and far
superior process variation solution. One that
is not simply a proven way to detect broken
mandrel links that can result from excessive
pull forces, but is also able to identify the
issues that result in such a force taking place.”
In the process variation system offered
by AddisonMckee and OES, the process
involves monitoring the pressure placed
on the mandrel during each and every
bend cycle. This is achieved via use of a
piezoelectric force transducer located at the
mandrel reaction component of the bender.
Any change in mandrel pull force or tension
that falls outside pre-set control parameters
is then highlighted as a process variation of
degradation. Variations can result from loss
of lubrication, galling, tube misalignment or
slippage, change in material hardness, or
even use of a material that falls outside of
specification.
Mr Rogiers adds,
“In simple terms, this
process monitoring solution acts by alerting
the process operator to any production
changes that might lead to mandrel failure.
This is unlike traditional mandrel failure
systems that may allow considerable
quantities of faulty components to be
produced before failure is detected. By
monitoring the pull force during the bend
and withdrawal stages, it becomes relatively
straightforward to maximize machine set-up
and reduce machine downtime.”
OES Inc
– Canada
Fax
: +1 519 652 3795
:
oes@oes-inc.comWebsite
:
www.oes-qualityassurance.comAddisonMckee
– USA
Fax
: +1 513 228 7226
:
crogiers@addisonmckee.comWebsite
:
www.addisonmckee.comHAEUSLER AG Duggingen
Baselstrasse 21
CH-4202 Duggingen
Switzerland
Tel.: +41 61 755 22 22
Fax: +41 61 755 22 00
sales@haeusler.com www.haeusler.comThe world market leader in tube and pipe technology
Please visit us:
Fabtech International & AWS
Welding Show in USA, 6. – 8.10.2008,
Tube & Pipe area, Booth 8202
Euroblech in Germany,
21. – 25.10.2008,
Hall 11 Booth F24
Increased component repeatability with
mandrel bend monitor
The mandrel bend monitor from OES and AddisonMckee