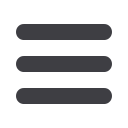

S
eptember
2008
www.read-tpt.com194
›
T
ube
B
ending &
E
ndforming
T
echnology
latest generation components to ensure a
very broad range of advantages.
Features include low power consumption,
high productivity, precision and repeatability
of the axes, left and right bending, and
pushed carriage for rolling. The machine is
capable of multi-height and multi-radius on
several levels and two tools. Other features
include ergonomic height of loading,
electronic crank for programming by
training, programming in force or position,
and memorized adjustments tools.
Silfax
– France
Fax
: +33 4 72 31 06 19
:
info@silfax.comWebsite
:
www.silfax.comLatest Crippa bending machine
with electric operation
Crippa, Italy, is the manufacturer of the
CA1132 bending machine, which is based
on the existing model CA532. With the
same basic structure as the CA532, which
bends metal tubes with a diameter up to
32mm, the CA1132 offers a number of
advanced features.
The CA1132 is a CNC machine with
11 axes controlled by motors with
digital adjustment. Unlike the CA532,
the CA1132 involves electric and not
hydraulic adjustments. In addition to
the existing axes adjustments – such
as tube progress, rotation on its own
axis, positioning, and bending head unit
movement – other movements are now
electrically adjusted.
The operator mainly works on the CNC
by setting and checking the adjustments
without touching the bending machine.
It is now possible to use CNC ‘software
keys’ that automatically avoid any wrong
movement that can cause possible damage,
interference or collisions.
There is a significant reduction of waste
during the presetting and testing phase.
In addition, there is the possibility to
perform micrometric adjustments – fine
adjustments that were not possible with
other models. This feature permits the
bending of smaller tubes, such as AGR
tube, where adjustment accuracy is
needed.
Crippa SpA
– Italy
Fax
: +39 031 760 244
:
info@crippa.itWebsite
:
www.crippa.it611D drivers (full digital technology). With
a high production rate (up to 95 per cent),
the machine is capable of hydroforming
different convolutes in one shot.
Machine features include an integrated
loading and unloading system, memorized
tools adjustment, reduced changeover time,
auto
diagnosis,
low
maintenance, and modem
connection (as option).
The company has also
developed
the
fully
electric SE 50 LR CNC
bending machine. With
10 axes, this machine
is designed for a tube
diameter of 50mm and
production of units from
one to one thousand.
The design of the SE 50
LR is associated with the
Silfax Group, France, is the manufacturer
of fully electric bending and endforming
machines. The company has recently
launched the SHD4N, a hydroforming
machine for corrugated thin wall tube
(application: EGR tubes/pipe fuel tank).
The SHD4N has 4 electrical numerical axes,
a Siemens 840D numerical control and
CNC tube bending machines with 13 axes
Fullstage Technologies, Germany, offers a broad range of reliable bending and cutting
equipment for the tube and wire industries. The company has manufacturing partners in
Japan, Taiwan and the US, enabling Fullstage to offer a wide range of machinery.
The company’s range includes CNC
tube bending machines from
Chiyoda, a Japanese market leader.
Equipped with as many as 13 axes,
these systems can bend tubes with
diameters up to 250mm.
Chiyoda and Fullstage also
offer a line of benders for very
tight radius (1D or smaller)
applications up to 200mm in
diameter. Automatic loading
and unloading capabilities are
available for each machine.
Fullstage also offers cutting systems from
Chiyoda designed specifically for coiled tubing, as
well as Japanese and US cutting machines that cut tubes
up to 65mm OD and provide solutions for extremely
small wall thicknesses (from 0.2mm).
Services include installation, regular maintenance and complete repairs. Fullstage is a
worldwide supplier with a current emphasis in Europe including Russia. The company
can provide an equipment solution that meets each customer’s individual requirements
(eg quality, productivity, manufacturer, price).
Fullstage Technologies
– Germany
Fax
: +49 8024 60834 29
:
info-europe@fullstage-tech.comWebsite
:
www.fullstage-technologies.com
The SHD4N hydroforming machine for corrugated thin wall tube
One of the Chiyoda
bending machines offered
by Fullstage
Comprehensive range of forming and bending machines
n