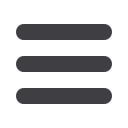

wire Southeast Asia 2011
93
wire Southeast Asia – BITEC, Bangkok 13
th
-15
th
September 2011
Lubrication is one of the crucial
factors for the quality of drawn wire.
An interrupted lubrication in the steel
wire drawing process causes an
increase of surface tension in the wire,
strong pressures inside the die, rapid
die wear, breakage of the drawing
nib and consequent non-programmed
interruptions in the wire drawing
process.
In order to avoid these problems,
Koner has studied a new concept
line of drawing dies: K.340 and K.370
pressure drawing dies (patented
worldwide), specially constructed and
designed to improve lubrication in dry
drawing of steel wire.
For wet drawing the K.320 tool has
been created, which allows with its
particular inside geometry optimum
wet drawing process characteristics
and also economic saving.
❍
Drawing die from Koner
The K.340/K.370/K.320 methods
provide operating advantages that
include production at maximum
drawing speeds; less machine down-
time for die replacement; better and
more homogeneous wire quality; wire
drawing under optimum quality control;
increased nib life; overall costs reduced
(only the nib is changed, rather than
the entire die); and application of the
requested quantity of lubricant coating
to the wire.
The overall dimensions of the K.340/
K.370/K.320 tools are the same as for
traditional dies.
Transport costs are reduced, as even
large quantities of nibs can be delivered
rapidly in small packages directly to
customers in any part of the world.
Koner Srl – Italy
Fax
: +39 0254 55832
:
tkt@tktgroup.itWebsite
:
www.tktgroup.itLämneå Bruk AB specialises in the
design and manufacture of machines
for the ferrous and stainless steel
wire industry and is a reliable supplier
of pay-offs, mechanical de-scaling
equipment, drawing machines and
take-up units.
For the solid welding wire industry
the company supplies complete lines
including pay-offs, cleaning equipment,
drawing machines, copper coating and
take-ups.
For tubular wire or flux core wire
Lämneå produces strip rewind lines,
strip pay-offs, forming-filling-closing
machines, drawing machines and
take-ups, in addition to high speed
rewinding lines including precision
layer and drum packer (no twist coiler)
for both solid and tubular wire.
For the low/high carbon and stainless
steel wire industry Lämneå supplies
rotating and/or over head pay-off
systems, mechanical cleaning units
(for carbon wire), drawing machines
and take-ups.
The take up systems range from down
coilers with controlled filling systems to
automatic spoolers.
Lämneå Bruk also makes pay-offs and
take-up systems for heat and surface
treatment of high and low carbon
wires as well as stainless steel wires,
take-up coilers with live block or dead
block depending on the requirements
of the process.
Lämneå Bruk AB – Sweden
Fax
: +46 122 232 99
:
info@lamnea.seWebsite
:
www.lamnea.seLukas will be introducing a vertical
taping machine, suitable for nearly all
types of tapes such as PTFE, Kapton,
mica, polyester, fleece, laminated tapes
and metal tapes.
The high speed and high precision
taping is enabled by a closed loop
tape tension control and a very precise
speed synchronisation between the
capstan and the taping heads.
❍
Vertical taping machine with sintering
oven
Depending on the application,
machines can be equipped with a
cooling unit for the taping area, inline
sintering oven or equipment for quality
control.
Lukas Anlagenbau GmbH –
Germany
Fax
: +49 965 930 299
:
lukas.voh@lukas-anlagenbau.deWebsite
:
www.lukas-anlagenbau.deMaillefer will present its portfolio of
extrusion systems for energy cable,
fibre optic cable, telecom cable and
tube manufacturing systems.
Visitors will see a series of continued
improvements in the area of rubber
cable insulation, filling and jacketing.
The Super steam technology can
provide a claimed increase in line
performance of 20, 50 or even 100%, in
relation to the type of cable produced
on conventional equipment.
When fibre optic cables made their
debut in the late 1970s, Maillefer was
present with equipment for the leading
players at the time. Today, Maillefer
provides high-end manufacturing
solutions for every stage of the fibre
optic cable process. Tight buffering,
secondary coating, SZ stranding
and jacketing lines are available for
producing all kinds of fibre optic cables
including premises and totally gel free
FTTx cable.
Technology like the compression
caterpillar with tension feedback serves
to keep accurate control of excess fibre
length.
➣➢➣
Maillefer SA
Stand F02
Koner Srl
Italian pavilion
Lämneå Bruk AB
Stand F11
Lukas Anlagenbau
GmbH
Stand H23