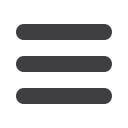

33
CONSTRUCTION WORLD
SEPTEMBER
2017
POLYMERS Wanother of their projects, into the 2016 CMA
Awards. The DF Malan High-School Multi-
Purpose Centre project was a 2013 Fulton
Awards Nominee.
More recently the company installed
200 mm precast concrete panels to the
brand new Reddam House School in
Durbanville. Nico said, “It was an honour
to be part of the construction of such an
amazing building which is situated right on
our doorstep. This school is a state of the
art development with the latest finishes and
facilities throughout”.
Future potential
“Using precast concrete slabs definitely
offers substantial savings in time. It is less
labour intensive for the contractor and
offers up to 30 days less standing time
on one simple deck. When we install the
panels, the client only has to fill the joints
and put a screed on top – that takes one
day. So while the cost of prefabrication is
not necessarily cheaper, the trickle down
on-site activities such as transportation,
labour and time are all either eliminated or
substantially reduced,” says Heyns.
Portland Hollowcore has two Elematic
Extruders and an efficient Elematic saw
assisting them to increase their production
of precast concrete panels. “Due to a
rising order book for our precast product,
we chose to airfreight the new Elematic
Extruder to South Africa. We needed more
capacity and quickly. While the costs to
do this were higher than sea freight, our
LEFT:
Cutting slabs.
RIGHT:
The V&A Waterfront parking area.
return on investment was within one
month of operation”.
Heyns highlighted the fact that the new
extruder enables them to manufacture 250
mm thick slabs, whereas before they could
only manufacture 160 mm and
200 mm thick slabs. The 160 mm slabs
are mostly utilised in residential housing.
“Our experience on the V & A Waterfront
parking project using our thickest sized
slab highlighted the potential for greater
applications for our precast concrete
products. The thicker the slab the longer
you can span, therefore making it suitable
for use in high-rise building developments
in Cape Town, as well as parkades and
office blocks. The Elematic Extruder
offers us extra capability and flexibility,
which in turn enables us to look at these
opportunities in addition to servicing the
social housing sector” she said.
Portland Hollowcore’s investment into
more advanced machinery enables them to
manufacture concrete panels throughout
the day, leaving the panels to cure overnight,
and be ready for cutting and delivery all
within a 24 hour window. “There is a better
quality product being manufactured now
that new processes have settled down. We
hold weekly quality meetings and conduct
quality tests in a controlled environment.
In our line of work there is no room for
error with our product, the consequences
could be catastrophic. We are an extremely
quality confident outfit,” said Heyns.
“We have a strong relationship with
Portland Hollowcore. Their factories have
a well-planned layout that will allow them to
expand their production when needed. Our
warehouse in Dubai ensures that we
are able to assist our South African
customer base quickly and efficiently,”
says Curt Lindroth, Area Sales Director for
Elematic, Finland.
“We hope to expand our production
facility shortly. We do intend to stay with
Elematic, their machinery is high quality
and their support and service is their key
differentiator,” Heyns concludes.
Hollow core slab production.