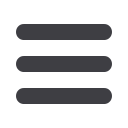

June 2015
Bricks & Paving
T
he South African designed,
developed and manufactured
machines have been in the
research and development (R&D
phase for 15 months and will now
add significant value to Hydraform’s
existing product portfolio.
The fully automated interlocking
brick and blockmakingmachines will
reduce labour production costs. Hy-
draform’s products aremanufactured
at its world-class facilities in Durban.
The new M7A2 automated block-
making machine produces interlock-
ing building blocks, suitable for load
bearing construction and walling.
The machine comprises a hy-
draulically operated hopper loading
system, three-phase electrical op-
eration, a loading platformand a 300
litre pan mixer.
“The M7A2 interlocking block-
makingmachine requires aworkforce
of between six to eight people to op-
erate and produces 6 000 blocks per
day,” says Nazlie Dickson, Sales and
Marketing Director for Hydraform. “It
is a two chamber system, operated
individually by two separate teams,
which means more efficient block
production per day.” Hydraform’s
second product – the convention-
al V4 hydraulic paving and block-
making machine only requires two
operators, which is significantly lower
than Hydraform’s previous machines
(excludingmixers and block carriers).
A fully functional block yard can
produce up to 15 000 blocks per day,
depending on the type of block being
produced.
The machine produces 120 drops
per hour and comprises of a double
vibration motor for high compaction
and increased quality, a three-phase
electric system fitted on a static
frame and an integrated 300 litre pan
mixer and skip chute mounted on a
platform. Fitted with interchange-
able moulds, the machine is ideal for
medium to large block yards.
“We realised that our machines
could be improved to push block
production for new markets and
current clients,” says Dickson. “Both
thesemachines have reduced labour
requirements that will ultimately
result in amore cost-effective block.”
In terms of technical support, a
dedicated after-sales support and
training department assists clients to
utilise the Hydraform product range
effectively. They will ensure that the
equipment functions optimally and
projects are executed successfully.
“The biggest challenge was to
develop an automated machine that
had the ability to go into urban cities
as well as rural areas. By roping in
the experts on the automation and
programming stages, we have man-
aged to overcome these challenges
and now have a simple, versatile
block-making solution, that despite
the use of automated technology, is
easy to fix, even in remote locations,”
says Dickson.
“In our market, construction is a
key component todeveloping and im-
proving the lives of people, communi-
ties and businesses. We are confident
that our new products will make it
easier for clients to deliver building
solutions,” concludes Dickson.
For further information contact
Hydraform on 011 913 1449 or visit
www.hydraform.com■
Automated
block-making
machines
Hydraform, a leading South African manufacturer of interlocking
brick and block-making machines, has recently launched two new
products to the South African building and construction market.