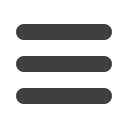

60
TUBE PRODUCTS INTERNATIONAL May 2014
www.read-tpi.comRidgid
– USA
www.ridgid.comRidgid has been manufacturing and
selling tools to the pipe working and
contracting industry since 1923, when it
was founded in North Ridgeville, Ohio,
USA, to manufacture a revolutionary
style of heavy-duty pipe wrench.
Since then, the company has developed
into one of the world’s largest suppliers
of tools to the professional trades.
As time passed, the company expanded
its product line to include many other
tools. In 1943, growth was such that the
company had to move its headquarters
to its current facility in Elyria, Ohio.
Ridgid manufactures over 300 different
tools in more than 4,000 models and
sizes, ranging from the original Ridgid
pipe wrench to pipe/tubing tools,
pressing tools for joining copper tubing,
pipe and drain cleaning equipment and
the latest diagnostic inspection and
locating tools.
The company’s products are distributed
on six continents and in more than 155
countries. Markets are served from a
125,000ft
2
central distribution facility in
central Ohio. Other stocking warehouse
locations include Europe, Canada,
Central and Latin America, Australia,
the Middle East, Japan, the Far East
and Africa.
Ridgid products are sold to end users
through professional tool distribution
and large retail channels. In the USA,
Ridgid tools are available at over 4,000
distributor locations.
The company manufactures products
on three continents to serve the world
market. The main manufacturing facility
and world headquarters are in Elyria,
Ohio, where pipe working products are
produced. Other US manufacturing
facilities are located in Erie, Pennsylvania,
and Orange, Virginia. Overseas
manufacturing facilities include Sissach,
Switzerland; Gevelsberg, Germany; Cluj-
Napoca, Romania; and Shanghai, China.
Step 7: Ream the pipe
Reaming of steel pipe is required by code. Removing
the steel burr (created when cut by a pipe cutter)
on the inside diameter of the pipe allows for
unrestricted flow of fluids, steam and wires that may
be intended to go through the pipe.
To begin the threading operation, ensure your
die head has the corresponding size of dies for
the diameter of pipe. Next, set your die head to
accommodate this size. As a reminder, threading
1
/
8
"
to 2" pipe requires four sets of dies:
1
/
8
" – 27 threads
per inch (TPI);
1
/
4
" to
3
/
8
" – 18 TPI;
1
/
2
" to
3
/
4
" – 14
TPI; and 1" to 2" – 11
1
/
2
TPI. The ream is completed
when you see the burr has been removed.
Step 8: Threading the pipe
To begin threading, pull the die head down so it sits on the
carriage. Prior to advancing the die head, start the machine
to begin rotating the pipe in a forward, counter-clockwise
direction. Next, advance the die head to the rotating pipe.
Apply pressure after the throat of the dies makes contact with
the end of the pipe. Note: the dies are designed to engage the
end of the pipe at this point. That is what allows you to cut the
thread under the power of the rotating pipe.
A standard-length thread is typically completed when the
last tooth on the dies comes flush with the end of the pipe.
This will give you a standard length of thread, allowing you
to manually thread on a coupling (approximately three turns,
using a pipe wrench to tighten completely).
As a special side note, it is important that you use quality
thread-cutting oil when threading. Not only will it lubricate
the pipe, allowing for the dies to cut through the material
with greater ease, but it will also perform a flushing function,
moving chips away from the work to minimise torn threads.
Additionally, threading oil ‘cools the work’, keeping dies from
heating up during metal-to-metal operation.
Finally, if threading various material types, it is important
that you use the best oil for the operation. Motor oils, lathe
coolants and water are not suitable for threading.
Step 9: Cutting the pipe
Once the pipe is threaded, cut the pipe to your desired length.
To do so, make sure the pipe is not rotating, then pull the pipe
cutter down on the carriage and place over the pipe. Close
the cutter wheel up to the wall of the pipe and begin rotating
the pipe forward. Once the pipe is moving, advance the cutter
wheel until it breaks through the inner wall of the pipe. (Note:
Do not stop rotating the pipe until the cut has been made
completely through its wall). Once the cut has been made, you
are ready to perform the next task on the uncut end.
Ridgid – company background