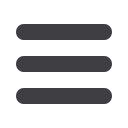

92
S
eptember
2009
www.read-tpt.com›
The Haventrak utilises the company’s dual-
blade shear cut-off head combined with a
Utrak™ length control system to deliver
dimple free cuts at speed, which provides
improved production rates with increased
accuracy of up to 250 FPM.
Haven Manufacturing says the machine
produces high quality cuts on a variety
of tubular shapes and materials utilising
the dual-blade shearing method. Universal
Controls Group, Perrysburg, Ohio developed
the Utrak length control system blending
hi-tech electronics and simple mechanics to
provide an accurate and rugged solution to
length control needs.
Website
:
www.havencut.comWebsite
:
www.universalcontrolsgroup.comHMT
USA
2042
HMT says it is revealing its most exciting
ever lineup of tube bending technology at
this year’s Fabtech.
The company says its Unison all electric
40mm Multi-Stack is one of the most
environmentally friendly benders available,
with its high precision state-of-the-art
control system, low heat during operation,
and minimal noise.
The Horn Metric Series CNC45EMR all
electric CNC tube bender has a rotatable
head that combines left and right hand
bending with triple stack tooling, which is
capable of push rolling and draw bending
all in one machine.
The HMT #4CNC-LP bender is a heavy-duty
CNC bender with a low-to-the-floor load
height. This puts the tube at a comfortable
and ergonomically correct height for the
operator without the use of work platforms.
The machine is equipped with direct acting
programmable clamp and pressure die to
reduce set-up time as well as Y axis boost
and a retractable wiper die.
HMT CAD File Import will be demonstrating
the ability to import Step files and other
CAD files directly into the bender control,
simulating the part on the screen and
then forming the part on the machine. The
company claims this unique ability allows
the part to go from design to production
faster than traditional methods.
Website
:
www.hornmachinetools.comInterlaken
USA
TBC
INTERLAKEN Technology Corporation
designs, engineers and manufactures
servo-controlled production equipment
with sophisticated controls and monitoring
software. The company will exhibit
hydroforming press systems for use in
productionormaterialsresearchapplications.
The computer-controlled hydraulic press
systems feature data acquisition that uses a
high-pressure liquid to hydroform materials.
The company’s hydroforming press systems
are designed for both tube and sheet
hydroforming applications. Gas forming
systems are also available.
The hydroforming press systems are
equipped with Interlaken’s UniPress control
system for reliable and precise control over
the hydroforming process. Easy to use,
Windows-compatible interface software
enables users to build motion and force
profiles designed to fit specific forming
needs.
The multi-channel, closed loop control
system is easily programmed to handle
event as well as time dependencies.
Interlaken’s hydroforming technology