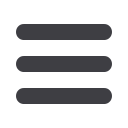

EuroWire – January 2010
54
Cleaning & descaling
Wet blasting process
Vapormatt Ltd has developed a compact, dedicated machine for the in-line cleaning
of continuous wire, rod and strip materials during manufacturing or post-production
operations.
The new Vapormatt 1210 machine is said to remove heat treatment oxides, lacquers,
oil and grease from the surface of the material more effectively than ultrasonic or
mechanical methods based on ultrasonic or mechanical systems, and is safer and
more environmentally acceptable than processes using harsh or potentially hazardous
chemicals.
The machine removes deep-seated contamination without damaging the underlying
substrate and eliminates the need for time-consuming pre-cleaning or preparation.
It can be installed into existing wire, rod or strip production lines.
The machine operates on a continuous basis, providing a simultaneous surface
preparation, degreasing and rinsing action, with the wire, rod or strip material passing
through the processing enclosure on a roller support system, via sealed entry and
exit apertures.
The processing enclosure incorporates a specially designed manifold, fitted with
preliminary wash, multiple wet blast and air blow-off nozzles to ensure all round,
thorough surface cleaning as the material passes through. An aluminium oxide-based
wet blast media is normally employed for the main cleaning action, although other
types of media can be used, depending on the particular application.
Because the wet blast process uses water and compressed air as the carrier for the
abrasive media it is less aggressive than dry blasting. With wet blasting, the water
acts as a buffer and lubricates the particles on impact, enabling very fine and smooth
finishes to be produced without surface damage.
The process is self-contained, with the machine working on a closed-loop basis; process
water is continuously filtered and waste material and debris is directed to a container
for regular removal.
Since no solvents or other potentially hazardous chemicals are used in the process,
the machine is not subject to strict solvent emission, VOC or dust emission legislation.
Vapormatt Ltd – UK
Fax
: +44 1823 336446
:
sales@vapormatt.comWebsite
:
www.vapormatt.comVapormatt’s 1210 machine
▲
▲