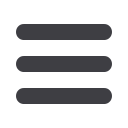

EuroWire – January 2010
66
Extruding – machinery & equipment
Continuous extrusion
of copper bus bar
Beijing Holland’s continuous copper extrusion machine model, TLJ400 will fabricate
wide cross section copper bus bar. With one size (20mm diameter) rod feeding, the
machine extrudes copper bus bar of 170mm width and 2,000mm
2
cross-section area.
The end products are widely used as large copper conductors, and semi-products of
copper strip and copper foil.
Testing and metal flow analyses have ascertained the optimum materials for die and
tooling, and the precise flow patch design to withstand huge friction and pressure
during extrusion. The feeding rod is not heated before extrusion, making the process
and operation easy.
Offering the convenience of easily sourced
20mm rod, continuous production,
different sizes of product, less scrap and
easy operation, the TLJ400 machine has
become popular with copper bus bar
producers, taking the place of traditional
hydraulic extrusion presses in some areas.
Over 100 machines have been installed
worldwide and a larger machine is in
development.
Continuous extrusion technology is also
suitable for the production of aluminium
cladding steel wires and aluminium
cladding cables.
Beijing Holland Tech Co Ltd – China
Fax
: +86 10 6803 2878
:
webmaster@bjholland.comWebsite
:
www.bjholland.comCopper extrusion machine TLJ400
▲
▲
Portal
machine
The Sampsistemi division of SAMP SpA
has a new generation of self-traversing
portal payoffs and take-ups to complete
the range of powerful machines for
cable extrusion.
Multiflex-25 is a multi-material extrusion
screw. The new portal machine’s maxi-
mum reel flange diameter is 5,000mm
for a maximum weight of 60 tons.
Each model has a very wide reel range; for
example, a 3,000mm (20t) model loads
reels with flange diameters between
900mm and 3,000mm and it runs at 300m
per minute.
Thanks to the wide bobbin range,
customers will need only a limited type
and number of spare parts.
All machines are engineered to increase
the production efficiency and don’t have
gearboxes, chains or belts for the power
transmission.
The SAMP payoffs and take-ups only use
AC motors for accuracy of the machine
movements.
In addition, the set-up time is said to be
much lower than the standard market
average.
The machine is extremely flexible due
to the beam telescopic device and a
new changeover system. SAMP recently
supplied Nexans with eighteen of these
machines.
SAMP SpA – Italy
Fax
: +39 051 370860
:
info@sampspa.comWebsite
:
www.sampspa.com