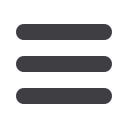

12
¦
MechChem Africa
•
August 2017
Chevron refinery
gets high pressure clean
Chevron’s refinery inMilnerton, CapeTown,
underwent its annual shutdown recently,
duringwhichhigh-pressure industrial clean-
ing of the plant and equipment was con-
ductedusing equipment fromSouthAfrica’s
leading water jetting solutions company,
Total Blasting.
Total Blasting director, Bradley Storer,
remarks, “Our client, who was commis-
sioned to oversee the industrial cleaning of
the Chevron refinery plant and equipment,
needed reliable rental pumps for the job,
because the bandwidth of their own equip-
mentwouldnot suffice for the scope of such
a project.”
Equipment supplied to the project by
Total Blasting to cleanheat exchangers, pipe
linesandprocesstanksincludedtheirT3and
T4 Series units, working at 1 000 bar at 50
to 100
ℓ
/min and 2 800 bar at 19
ℓ
/min,
respectively.
Both T3 and T4 Series units are suit-
able for demanding applications and
for single or twin-gun operation. Most
common applications include clean-
ing, descaling, coating removal, pipe
cleaning, marine growth removal, floor
cleaning and heat exchanger cleaning.
“Of paramount importance for a
project of this size and measure is both
the supply and quality of equipment, which
in this case, included high pressure pumps
and associated tooling. It is essential that
all of the equipment supplied runs without
any breakdown to ensuremaximumuptime
during a short maintenance window,” says
Storer, adding, “At Total Blasting, we ensure
the highest possible rates of uptime by sup-
plying thebest andmost suitableequipment
we have, alongwith excellent technical sup-
port to back it.
“Welookforwardtoarepeatpartnership
in the near future, when our rental fleet
and technical team will be commissioned
to support both the Sasol Secunda and
Natref refinery shutdowns later this year,”
he concludes.
q
“
T
his custom-engineered, one-of-
a-kind machine is capable of ac-
commodating crankshafts with
lengths of over six metres,” says
Andrew Yorke, operations director at Metric
Automotive Engineering. “It represents our
philosophy of investing in the latest bespoke
and best practice technology, so that we can
offer our customers around Africa a world-
class standard of service.”
Yorke says that while crankshafts have
traditionally been ground and then polished
on grinding machines, this is certainly not
the ideal solution. “Polishing debris con-
taminates the crank grinding machine and
this can lead to accelerated wear on critical
areas of the machine,” he says. “Moreover,
not all crankshafts need to be both ground
and polished; some only need polishing, and
doing this on a grinding machine is not the
best use of this asset.”
Metric Automotive Engineering’s dedi-
catedpolishingmachinewill significantly raise
the company’s productivity, enabling even
more rapid turnarounds on those crankshafts
that require only polishing and not grinding.
“We will also employ this machine to pol-
ish camshafts after the re-profiling of the
component, or if the journals and lobes only
require a polish and not a re-profile,” says
Yorke. “Polishing of these components after
Africa’s largest
crankshaft polisher
Total Blasting’s
T3 and T4 Series units.
Metric Automotive Engineering’s custom engineered, one-of-a-kind
crankshaft polishing machine is capable of accommodating crankshafts
with lengths of over six metres.
Metric Automotive remanufactures heavy diesel
engine components for a range of different end-
user industries and has developed a long and
impressive track record over almost 50 years.
With the installation and commissioning of the largest crankshaft
polishing machine in Africa, leading diesel engine component
remanufacturer Metric Automotive Engineering is once again
ahead of the curve.
grinding is vital, as it
removes grinding burrs
and ensures that the
surface finish is ideally
matched to the require-
ments of the bearing
materials they run on.”
He emphasises that,
in the case of crank-
shafts and camshafts,
therearejournals,which
run on the bearings and lobes, which have
roller followers carrying high loads. These
require the best possible surface finish in
order to prevent roller skidding or seizure.
“By polishing these journals and lobes
to the correct surface finish, we can return
themtoOEMspecification or better,” he says.
“In turn, this leads to improved component
performance and longer engine life.”
MetricAutomotive remanufactures heavy
diesel engine components for a range of dif-
ferent end-user industries andhas developed
a long and impressive track record over al-
most 50 years. It has generated its extensive
capabilities by staying abreast of the latest
global developments in diesel engine tech-
nology. To ensure the highest standards and
expertise, it also maintains close affiliations
to the leading diesel engine OEMs.
Repairing and remanufacturing modern
diesel engine components to their original
OEMspecification is an exacting science, says
Yorke. “It requires long-term development
of expert skills and ongoing investment in
specialised equipment such as this state-of-
the-art polishing unit,” he concludes.
q