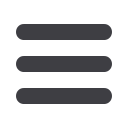

sustainable construction world
6
“It is clear that sustainability is today a fundamental
design requirement across the board in construction,”
says John Barnard director of the Southern African Light
Steel Frame Building Association (SASFA).
According to Barnard sustainability with regard
to buildings is essentially based on three criteria:
social acceptability, affordability and energy efficiency.
He claims that Light Steel Frame Building (LSFB)
for low rise structures – and increasingly for multi-
level structures – rates highly on most or all of the
sustainability considerations:
• Light steel frame buildings appear no different to
‘conventionally’ built structures, except that the quality
of finishes is typically better with the former. It has
found rapidly growing acceptance for ‘affordable’ as well
as up-market buildings in South Africa.
• It is a cost-effective building method, with financial
savings emanating mainly from significant time
savings to complete building projects, less rework,
reduced logistical costs –which are of growing
importance due to the escalation of fuel prices and
general construction inflation – and a drastic reduction
of rubble on building sites, when compared with the
brick-and-mortar alternative.
• Light steel frame building is significantly more energy
efficient than heavy construction methods – both
with regard to ‘embodied energy’ of the materials and
components, as well as ‘operational energy’ relating to
heating and cooling of the building over its design life.
Embodied energy
Barnard says that embodied energy of materials and
Alternative building methods
LSFB
– the most sustainable
construction method around?
‘Sustainability’, ‘energy efficiency’, ‘green
building’ and ‘carbon footprint’, are words
that were not so long ago regarded as
‘things for the future’ in the construction
industry. Well, the future has arrived.
components used for LSFB is reported to constitute
some 20% of the total energy consumption of a 200 m²
house, over a 50 year period, the other 80% being the
operational energy.
“While the embodied energy of the high strength
galvanised steel sheet – used for the light steel frame
– is significantly higher per kg than masonry building
materials, a significantly lower mass of steel is used
per unit area of building, rendering LSF wall assemblies
superior in this regard – based on Australian research,
double brick walls contain more than four times the
embodied energy per square metre when compared
with a LSF building.
He adds that the low mass of light steel frame
buildings offers another advantage – logistics. “The
walls of a 200 m
2
brick built house will have a mass of
some 178 tons including clay bricks, mortar and plaster,
compared with the 10,2 tons of an identically sized light
steel frame building. The cost savings in transport is
obvious, but with another benefit to all road users
– a huge reduction in heavy transport traffic on the
national roads.
Also, says Barnard, LSFB structures are insulated
to specification pertaining to each climatic zone in SA,
according to the new SANS 204, they have been found
to offer significant saving in electricity used for heating
and cooling, when compared with a brick building.
Clients in agreement
Many blue-chip companies agree, including both Burger
King and McDonalds. Charl van Zyl, CEO of Silverline
Group, who are building LSFB outlets for both of these
iconic companies says that the fast-food chains are
using LSFB because they support sustainable building
methods as far as design, energy efficiency and the
optimal use of natural light is concerned and because,
by using LSFB, material wastage can be reduced by up
to 30%, transport costs by 80% and the carbon footprint
significantly reduced.
“On top of this, the construction period required
is significantly less than with traditional building
methods, allowing the franchise to be trading that
much quicker,” Van Zyl says.
Meanwhile LSFB as a building method continues
to grow rapidly not only in South Africa but also in the
entire SADC region. “SASFA is receiving an increasing
number of enquiries from neighbouring countries and
has now signed up members in Namibia and Zambia,
and is in contact with several other countries in the
region. Overall the LSFB market is growing significantly
and indications are that this trend will continue into the
future,” Barnard concludes.
∞
John Barnard, director of the
Southern African Light Steel Frame
Building Association.
The entire turnkey project of the
Norwood Burger King took an incredibly
short 12 weeks to complete.