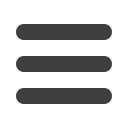

38
N
ovember
2010
www.read-tpt.com›
T
echnology
U
pdate
SEUTHE® Tube Welding and Section Lines
As an international plant engineering and manufacturing
company, we provide you with expertise that is backed by our
extensive experience and our product solutions to ensure
an optimum utilization of your production process.
In everything we do, we have one thing in mind: to help
you best to achieve your goals.
Call us + 49 2372 506 0 or
info@seuthe.comSEU_Anz_Tube+Pipe_09_2010
.qxd:Layout1 23.09.2010 12:47 Uhr Seite 2
RingSaw
®
is Reika’s new Generation of
machine tools for cutting of tubes, bars
and profiles with diameters ranging from
10 to 610mm and wall thickness from
1 to 150mm. The machine is operated
completely electro-mechanically without
hydraulics and therefore oil-free. The
cutting process is either dry, with mini-
coolant or flood emulsion.
No additional foundation work is
necessary (apart from machine fixations),
as the machine bed is totally oil-free and
designed as a closed cold water draining
and reservoir area. The chip conveyor can
be integrated directly into the machine
bed. The RingSaw will be delivered with
automatic tool changer (option) and totally
enclosed machine design with safety
protection cover according to state-of-
the-art machine tool style for full operator
safety and environmental protection.
Andreas Zimball, sales manager of
Reika company, is not surprised by the
tremendous demand for the new whirling
machine for tubes and bars. “If you know
this market then it is obvious that the
RingSaw is a better solution in nearly
every measure.”
The RingSaw can almost silently cut
bearing blanks from high grade, heavy
wall, large diameter feed stock. But
customers have also been impressed by
the basic motions of the machine with the
cutting ring whirling around the stationary
workpiece, resulting in tool cost savings
of 50% to 80% compared to conventional
carbide saws and a performance being
30% to 60% higher.
“We are talking about high six-digit
amounts that can be saved year by year,”
Andreas Zimball explains. “That means
investment cost for the RingSaw can be
paid off in a short time from tool cost
savings alone.”
Reika’s RingSaw is a completely
new designed line for cutting of tubes,
profiles and bars but that design is based
on decades of experience in intelligent
technology and know-how, shown by a
considerable number of similar concept
lines already well established on the
market. “This machine is far from being a
prototype – it is a trailblazer”.
The new concept is based on a
successfully proved project, originating
from Reika’s German competitor, Procon.
Reika, a member of the innovative
Graebener Group with more than 300
employees, including 80 mechanical
and electronics engineers, acquired the
Procon-Lines in 2009. Based on the
already existing Procon-Whirling lines
and using Graebener Group’s engineering
capacities, Reika successfully developed
the RingSaw.
According to the first case studies and
reports covering the RingSaw, a well-known
German manufacturer of roll bearing rings
achieved great savings in operating cost by
approximately 80% on the Reika machine,
compared to a conventional carbide saw
and with 30 to 60% higher performance,
and other manufacturers have also been
experiencing similar excellent results.
Reika GmbH & Co KG
– Germany
Email:
info@reika.deWebsite:
www.reika.deReika’s new cutting line reducing tool