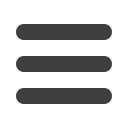

68
N
ovember
2010
www.read-tpt.com›
T
echnology
U
pdate
Welding
innovations
EWM Hightec Welding exhibited at this year’s
EuroBLECH fair the latest equipment and
process innovations from its research and
development team: alpha Q, Taurus, Phoenix,
rootArc
®
and pipeSolution
®
. The company
also presented its range of products, from
high-tech power sources to torches and an
updated range of filler materials.
In addition to the process versions
forceArc
®
and coldArc
®
, theMIG/MAG inverter
welding power source alpha Q can now also
handle the new pipeSolution. This brand new
process demonstrates its advantages in the
construction of pipelines, pipe systems and
pressure vessels: quick and dependable
MAG root welding with high quality, whether
for manual or mechanised welding (eg orbital
technology), with or without an air gap,
on unalloyed or low alloy steels, with solid
wires.
The arc is especially powerful and
therefore directionally stable no matter what
the thickness of the material, and in all
positions of the sheet or the pipe. Once the
root has been welded, the alpha Q changes
the process on demand and welds the filling
layers and the final pass with a pulsed MAG
process. This innovation is an economical
alternative to TIG welding.
The economic advantage of the welding
process is additionally increased if the
power source is equipped with a twin case,
eliminating the need for a conversion of the
filler wire and shielding gas or a second
machine. The repertoire of the alpha Q also
includes standard MIG/MAG welding TIG
(Liftarc) and the MMA welding process.
The possible applications of the Taurus
power source have been extended: the
Taurus Synergic series can now also handle
welding with forceArc and is equipped
with the rootArc process. This innovation
features a stable, soft short arc – suitable
for simple and dependable root welding,
easy bridging of the seam gap and out-of-
position welding.
The new, compact Phoenix 335 puls with
integrated wire feed supplements the Phoenix
range of fully digital inverter welding power
sources. Thanks to the plastic casing, the
unit is now more ergonomic and significantly
lighter. Equipped for almost any welding task
and especially convenient and easy to use,
the Phoenix is suitable for use in construction
sites, assembly work, workshops or production
halls. In addition to the previous MIG/MAG
pulsed and standard processes, forceArc,
TIG (Liftarc) and MMA welding, it now also
operates with the rootArc process version. The
Phoenix 335 is easy to use and control, and
can be simply extended with a cooling module
and a transport vehicle, without any tools or
special knowledge.
The effectiveness of a process chain
is determined by all of its components.
For this reason EWM carries out its own
development and production of MIG/MAG
torches. The EWM torch standard, which
was first presented at the last EuroBLECH,
has now demonstrated its worth in practice.
Users report that the optimised geometry
of the EWM contact tip (M7 to M9) ensures
excellent heat dissipation and perfect current
transfer. The tip remains cooler and the
extremely low spatter formation of the EWM
process is significantly reduced. Reworking
is reduced even further and the service life of
the wearing parts is also extended, which in
turn has a positive effect on both changeover
times and production costs.
For mechanised welding, the company
supplies new AMT series torches with
various angles for currents from 220 to
550 amps. The wearing parts of the torch
are identical to those of the hand torch and
are therefore of the same quality. Process
reliability and a long service life of the
contact tip are especially important with
mechanised welding. Each interruption of
the welding process causes a standstill of
the system, which results in great losses of
production.
EWM Hightec Welding GmbH
– Germany
Fax: +49 2680 181 244
Website:
www.ewm-group.comIntegrated tube processing equipment
EWM AMT series torches
Tube processing equipment from Euromaquina
EUROMAQUINA, Spain, offers integrated
tube processing equipment from the coil to
the galvanised pipes in bundles. Using the
latest technology, together with its partners
the company can now provide integrated
solutions as turnkey projects, such as
mother tube production, stretch reducing
mill (hot rolling), galvanising, threading,
packaging or shot blasting-galvanising.
Increasingly present in the Middle East,
the company now also has offices and
agents in ASEAN countries.
The company’s key concept is not to
consider steel construction, tube making,
galvanising and material handling as
independent issues, but to look for the
best possible product design and process
flow in terms of durability of final structure
(product), reuse of valid mechanical and
thermal components of actual plants
(investment budget), and looking at
the feasibility of automatic galvanising
(efficiency) and avoiding non value-adding
steps.
Euromaquina SA
– Spain
Email:
info@euromaquina.comWebsite:
www.euromaquina.com