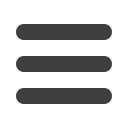

84
N
ovember
2010
www.read-tpt.com›
C
utting
, S
awing
& P
rofiling
Production Excellence, Logistic Support
and Project Partnership are perfect
examples of the ERNE qualities and skills
documented by certifications and translated
into international projects and references
from satisfied customers the world over.
erne fittings gmbh,
6824 Schlins, Hauptstrasse 48,
Austria/Europe,
office@ernefittings.com,ernefittings.com
better fittings. best connections.
Conair increases
accuracy on
new line of
cutters
A POSITION-based servo drive system,
which is now standard equipment on the
newest Conair flyknife cutters, increases
cut-length accuracy by as much as 1,000%.
At the same time, the CSC Series cutters
carry a price tag that is almost 20% lower
than similar cutters, the company said.
Designed for applications involving
extruded profiles and tubing, the CSC
Series cutters are available in 2-, 3-, 4- and
5-inch-diameter cutting capacities. Units
can make up to 350 cuts per minute in
on-demand cutting mode, or up to 4,500
cuts per minute in flywheel mode. The new
cutter line underwent a full year of testing
to ensure performance and reliability before
being released to the marketplace.
The standard positional servo drive
system provides cut response repeatability
within ±0.1 millisecond – a ten-fold
improvement over conventional velocity-
based servo systems, which are capable
only of repeatability within ±1.0 millisecond.
Cut response repeatability relates directly
to product cut-to-length accuracy, with fast
response becoming especially important as
extrusion rates increase.
An eye-level control panel, with soft
numeric and fixed-function keys, is the
operator interface to the CSC Series control
system, which, along with the servo drive,
is the secret to the cutter’s accuracy. The
system features a multi-tasking motion
coordinator instead of a more conventional
preset counter. Built right into the servo
system, the motion coordinator measures
length directly rather than depending on
readings coming from a separate counter.
The primary benefit of this control system
is the virtual elimination of “latency time” —
the amount of time required for the program
loop to monitor incoming length information,
check it against the programmed length,
and signal the cut. The control system
delivers other benefits, including:
Real-time repeatability tester: built-
in to confirm cutter accuracy. The tester
automatically measures repeatability of
the blade park position in milliseconds, to
three decimal points, and even differentiates
between variations arising from the input
devices like encoders, electric eyes and timers
and feed devices such as belt pullers.
Multiple cut-length actuation modes:
including counter/encoder, timer, flywheel
or end sensing.
Auto-demand cutting mode: gives users
the ability to vary the blade speed and
increase the cuts per minute. Besides the
accuracy of the control system and the
position-based servo drive, other features of
the CSC Series servo drive set it apart from
other units. These include:
In-line planetary gear reducer: unlike
more commonly used belt-and-pulley
reducers, planetary gear reducers
are designed to be directly mounted to
servomotors. They tolerate axial and radial
loading better and protect the servomotor.
4:1 reduction ratio: compared to belt-
and-pulley systems, which typically achieve
a 2.5:1 reduction ratio, the CSC cutters can
provide more cutting torque while extending
motor life. For high-speed, light-duty
applications, which don’t require as much
torque, the Model CSC-L can be supplied
without the planetary reducer.
Available 2.7- and 3.8-hp drives: deliver
torque ranging from 620 to 906 inch-
pounds.
Intercept
algorithm:
optimises
repeatability by compensating for firmware
scan time variations and readjusting
velocity and position, taking actual scan
time variation into consideration.
Aluminium and stainless-steel cutting
heads are available for (respectively) high-
speed cutting and applications requiring
high-torque.
Conair
– USA
Website:
www.conairgroup.comLarge diameter
fittings saw
ADESCOR Inc, Canada, has developed a
plastic fittings saw for diameters from 450
to 1,800mm and upwards. The machine
features a vertical reciprocating motion with
a 200mm wide blade and a guide that
follows the contour of the pipe providing extra
stability. The saw blade head arrangement is
mounted onto a right and left pivoting head
that moves into a clamped pipe.
Adescor has also unveiled a new semi-
automatic slab cutter that provides a cost
effective means of cutting large diameter
misformed pipe into strips for feeding into
a grinder. This new machine takes a 2m
length of corrugated pipe and cuts the pipe
longitudinally into 300mm wide strips.
The operator rolls the 2m section of pipe
into the slab cutter, which activates the safety
light barrier and the slab cutter cuts a section
of pipe, ejects the cut slab, rotates the pipe
for the next cut to be made, and continues
the process until the pipe is cut up.
Adescor Inc
– Canada
Fax: +1 519 520 8614
Email:
sales@adescor.comWebsite:
www.adescor.com