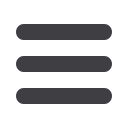

27
CONSTRUCTION WORLD
JUNE
2016
Pumping technique can also contribute to exacerbating the situation
and the hopper should always be completely full to ensure that air is
not sucked into the pump and that a constant pumping pressure can
be maintained. It is also important that the integrity of the equipment
being used is sound as a leaking pump or pipes will introduce air and
affect the pumping pressure.
“It is vital to look at the concrete pumping application and deter-
mine the most appropriate admixture that will fulfil the requirement.
This will also ensure the integrity of the final concrete product,” he says.
Use of chemical admixtures means that concrete can now be pumped
under a broad range of conditions, and this includes farther, higher and
faster than previously possible. Admixtures also enhance the physical
properties of the hardened concrete.
Correia says that adjusting or changing the admixture selection
can facilitate the required properties for pumping. “It is also important
to understand that one superplasticiser will not suit every concrete
application or type of cement as each is specifically designed to achieve
a maximum performance with a certain type of cement chemistry,”
Correia says. He again points to the need for construction companies
to work with reputable material and chemical admixture suppliers to
ensure that a fit-for-purpose concrete mix design is achieved that will
fulfil the specific project requirements.
Examples throughout the world
A good example of a project where Chryso® Fill Free® technology is
being used is the World One residential buildings in Mumbai India. At
a height of 442 metres, these will be the tallest residential buildings in
the world and the high strength concrete superstructure, with 100 MPa
walls, uses the innovative Fill Free® admixture technology. Correia says
the extreme pumpability offered by the product is ideal for such a super
tall structure.
Local examples of projects that have used Chryso® admixtures to
achieve concrete pumping success are the Impala Platinum No 16 shaft
and the Michelangelo Towers.
At the time of construction, No 16 Shaft was the tallest mining
headgear in the world with its structure reaching 132 metres high with
109 metres above the ground. With wall thicknesses between 550 mm
and 950 mm, the shaft structure has a width of 20 metres and a breadth
of 21 metres. Construction was achieved using slip forming method-
ology and Chryso® Fluid Optima 100 was used to give the mix extended
workability without affecting the setting time.
Correia says that this enabled the contractor to speed up the pace
of construction and resulted in cost savings on the project.
Chryso® Omega 140 and Chryso® Optima 100 was used during the
construction of the Michelangelo Towers. This admixture was selected
to reduce pump pressure which facilitated pumping of the concrete to
the top of the structure at 143 metres.
It is vital to look at the concrete pumping application and determine the
most appropriate admixture that will fulfil the requirement.
RES