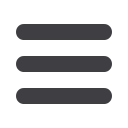

News
Technology
September 2017
53
www.read-eurowire.comMHD (magneto-hydro-dynamic) galv-
anising technology is claimed to be the
only eco-friendly galvanising process on
the market today.
SunWyre offers economical and environ-
mentally friendly galvanising solutions for
rod, wire, rebar, pipe and tubing.
SunWyre’s modern process is for high
or low carbon steel wire rods or wire, 4
to 16mm diameter, moving at speeds
from 1.7 to 5m/sec automatically and
continuously through galvanising and
drawing, non-stop.
The skilful integration of continuous
rod pay-off, blast cleaning, induction
heating, MHD galvanising, quenching,
wire drawing and coiling or spooling, all
managed by touch-screen PC, provides
an efficient continuous process for
galvanised wire manufacturing.
SunWyre’s proprietary MHD process
offers the following advantages over
traditional hot dip galvanising:
•
It is energy efficient
•
Energy costs to maintain only one
ton of zinc, instead of 50 or more,
are lower than traditional wire
galvanising
•
7kW or less will maintain the pot
temperature when the system is idle
•
Non-polluting
•
Uses no acid or flux
•
Requires no waste water treatment
system
•
Emits no toxic fumes
•
Creates no hazardous by-products
•
Offers lower operating costs than
traditional hot dip galvanising
•
Fewer man-hours are required to
operate the process
•
Low nitrogen consumption compared
to conventional gas wipe methods
The SunWyre MHD process offers an
innovative approach to the production of
galvanised and galfanised steel wire.
The process creates a wire with superior
formability and corrosion resistance and
is non-polluting and energy efficient.
Capital and operating costs are lower
than traditional hot dip galvanising.
SunWyre Inc – USA
Website
:
www.sunwyre.comSunWyre’s
clean
galvanising
solutions
▲
▲
MHD Power Supply, coils and cooling system