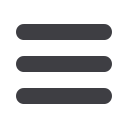

business & market news
10
Tube Products International May 2016
www.read-tpi.comRemoving hydrofluoric acid
from the pickling process
Started in 2014 and part-funded by
EU, through the LIFE programme, the
three-year project HFreelifepickling
aims to eliminate the use of hydrofluoric
acid in the pickling process used to
make corrosion-resistant large tubes for
building pipes for the oil and gas sector.
The companies that have promoted
and developed the project are Rivit,
an Italian manufacturer of pipes and
fittings in stainless steel and special
alloys, and Henkel, a German chemical
multinational, together with a public
body – the Province of Vicenza – whose
main task is verifying performance with
respect to environmental impact and
health of workers.
The first phase has particularly involved
the Italian laboratories of Henkel in the
province of Milan. For around a year,
the chemical company has researched
a new electrolytic solution that would
allow effective pickling without the use
of hydrofluoric acid – a component
almost always present in the treatment
system of this class of materials. A
problem that presented itself initially was
linked to an early ageing of the solution,
with the consequent increase of waste
for the replacement of the tank and
the production of sludge for disposal.
The quantity of sludge, following the
improvement of the procedure, became
comparable to that obtained using the
traditional process. Thanks to these
initial studies, the use of hydrofluoric
acid in the pickling process has been
eliminated, and on a laboratory scale,
the process also recorded a decrease in
working time of 70 per cent.
Following a successful test phase,
the project continued with the pilot
phase. In October 2015 Rivit proceeded
with the construction of a mini-plant
for testing, in order to verify the new
process and the electrolytic solution on
non-flat samples, taking into account
the geometric factor, which could cause
problems of electrical fields tangential
to the surface, and their response on
different families of alloys. The small
plant has allowed a more accurate
estimate of the effectiveness of the
treatment on the tubular geometry
and the powers in play. As a result of
these tests, the partners obtained the
fundamental measurements in order to
minimise the energy consumption and
to study the best design for maximising
the production capacity of the pilot plant
that will be built by the end of 2016.
HFreelifepickling will end in mid-2017.
The main innovation of the project will
favour a lower environmental impact
on a large scale. It will ensure greater
safety for operators employed in pickling
departments, and a reduction in working
time of 70 per cent.
HFreelifepickling
– Italy
www.hfreelifepickling.euRivit SpA
– Italy
info@rivit.com www.rivit.comHenkel AG & Co KGaA
– Germany
www.henkel.comThe mini-plant for testing the new pickling
process without the use of hydrofluoric acid
Henkel, Rivit, Province of Vicenza and European Union representatives at the Henkel
headquarters in Milan, in October 2015
Weld Revolution director
Weld Revolution has announced the
appointment of BryanGeorge as director,
business development, reporting to Eric
Christofferson, president.
As a member of the executive team
at Weld Revolution, Mr George will be
responsible for identifying and leading
strategic business development, in
addition to implementing commercial
strategies and strategic alliance
opportunities for Weld Revolution in
the USA, Canada and Mexico.
He has more than thirty years’ experi-
ence in the welding industry.
Weld Revolution LLC
– USA
info@weldrevolution.com www.weldrevolution.comBryan
George