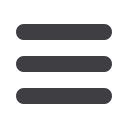

I NDUS T RY
www.read-tpt.com18
SEPTEMBER 2017
ESAB to demonstrate high-tech welding
ESAB Welding & Cutting will be on
stand 10F04 in Hall 10 at Schweissen
& Schneiden, which takes place in
Messe Essen, Germany, from 25 to 29
September 2017.
The company will have a number
of high-tech products and systems
on its stand, many of which will be
demonstrated live so visitors can
see them in action for themselves.
Knowledgeable, experienced staff will
be on hand to explain the technologies
and discuss end-user applications.
ESAB will have live demonstrations
with its new Excellerator pre-engineered
robotic cell, which will show various
MAG welding processes as well as
featuring ESAB’s Swift Arc Transfer
(SAT) high productivity welding process.
ESAB
will
also
have
live
demonstrations of the Gantrac 300
gantry-based welding system with ICE
submerged arc welding (SAW) and
Aristo
®
1000 AC/DC power sources with
Marathon Pacs of wire and BlockPacs of
flux. Demonstrations will be performed
both with automated spiral cladding
and welding, both in narrow and normal
V-joints. Further live demonstrations
will include high-deposition cladding
with 60mm stainless steel strip. ESAB
will also display a number of different
welding tractors, welding heads and
accessories for automated welding.
A major focus of the ESAB stand
will be automated bevel cutting; there
will be live demonstrations of both the
new DMX automated plasma beveller
and the three-torch global oxy-fuel IR-
VBA. Both systems are installed on
ESAB’s new Suprarex HDX heavy-duty
large gantry cutting machine, which will
also be equipped with ESAB’s iSeries
plasma system.
The new DMX automated plasma
beveller is a reliable, easy-to-use,
compact bevel system designed for
safe, high-quality plasma bevel cutting.
DMX offers enhanced reliability and
advanced collision sensing that easily
detects and absorbs a torch crash, then
automatically resets without touching
the torch. This non-breakaway system
enhances operator safety by eliminating
dangerous operator tasks.
The compact DMX design can be
mounted on smaller gantries, making
bevel cutting more affordable and
saving valuable floor space. DMX also
includes SmartBevel Technology to
simplify bevel programming and deliver
consistent, accurate results.
The three-torch global oxy-fuel IR-
VBA is used for complex bevelling on
thicker mild steel plate.
The infinite rotating system features
programmable bevel angles and
offsets, which can change on-the-
fly in order to cut variable bevels, or
automatically change bevel geometry
during a program. This design offers
high productivity for customers cutting
complex bevels on mild steel up to
75mm thick.
The iSeries is an advanced power
supply, providing cost-performance
benefits and with customers having
the option to upgrade the unit as their
requirements grow and they need
more cutting power. Also incorporated
within iSeries systems, the Water Mist
Secondary (WMS
®
) process produces
superior cut quality and a lower cost-
per-cut on non-ferrous materials.
ESAB Welding & Cutting
– UK
Email:
info@esab.co.ukWebsite:
www.esab.co.ukCommissioning and ramp-up of hot leveller
ARCELORMITTAL Galati has commis-
sioned and finalised the ramp-up of
the new hot leveller serving its heavy
plate mill no 2. This project was part
of an extensive technical upgrading
programme currently underway at the
rolling mill and at the steel melting shop.
“This investment solidifies our position
in the plates market as we can now
deliver new and better products with
better services for customers,” said
Bruno Ribo, chief executive officer of
ArcelorMittal Galati. The new plate
leveller replaced a machine that had
been operating for more than 30 years,
increasing the overall performance in
terms of productivity, quality, consistency
of flatness in the finished products and
operational safety.
With 80 per cent more levelling
power and advanced automation, the
new Danieli hot leveller also ensures
the production of a higher range of
thicknesses and qualities for plates
used in applications such as energy
pipes, shipbuilding and construction.
The project and construction works
were carried out without disruption to
ongoing production, and without any
safety issues.
ArcelorMittal is currently operating
another Danieli high-performance hot
leveller installed at Gijon plant, in Spain.
Danieli SpA
– Italy
Website:
www.danieli.comTraining to use use the ESAB equipment