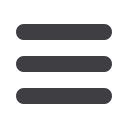

T E CHNOLOG Y
42
SEPTEMBER 2017
Duright grows following investment
in BLM all-electric benders
UK-based Duright Engineering is a tube
cutting and processing sub-contractor
and was an early adopter of laser tube
cutting in the UK.
The family-owned business is
looking to continue its growth strategy,
so managing director Ross Taylor
decided to diversify and expand the
tube bending side of the business. This
has resulted in a significant increase
in turnover in the last financial year
since the addition of two BLM Elect all-
electric tube benders.
“We are well known across our key
industry sectors of automotive, rail,
agricultural equipment and shopfitting
for our tube laser cutting capabilities and
we could have opted to expand further
on this, but as tube laser accounted for
70 per cent of our business we wanted
to opt for a different strategy, and tube
bending, particularly larger diameter
tube bending, provided an opportunity
to become a single-source option for
a lot of customers, providing laser and
bending under the same roof,” said
Mr Taylor.
Duright already operates four BLM
tube laser machines 24 hours a day
and six days per week. The latest of
these is the Adige LT Fiber tube laser
systems. This combined laser capability
allows Duright to process round tube
up to 154mm and square rectangular
tube up to 120mm section in lengths up
to 8.6m.
Duright was one of the first in the
UK to adopt fibre optic laser and it is
unusual for the tube sector to be leading
the flat sheet sector, but when it came to
fibre laser the tube industry was ahead
of the curve. “We had our first fibre laser
from BLM four years ago and we are
surprised that people still buy CO
2
tube
lasers as we cannot see any downside
with fibre, especially on the mix of
materials that we are cutting.”
After reviewing the market, the
company spotted opportunities to
develop by bending larger diameter
tube. The decision, therefore, was taken
to invest in two Elect all-electric, multi-
stack tube benders from BLM. The first
to be installed was an Elect 102 machine
with capacity to bend tube up to 102mm
diameter with a wall thickness up to
2.5mm. This was quickly followed by an
Elect 130, which can bend up to 130mm
diameter and 3mm wall thickness
material. There are many advantages
to an all-electric system, namely the
elimination of hydraulics, lower power
requirement, improved machine setting
and component quality.
“Competition is tough in the small
diameter tube bending sector and
chasing that volume work was not of
interest to us,” said Mr Taylor. “However,
there are few companies that have
invested in larger capacity tube bending
and we could see the benefits of going
after what may be smaller volume work
that would provide better margins.
I would say that we have reduced set-
up times by between 50 and 70 per cent
compared to our old hydraulic machines,
but the biggest advantage that we have
seen is in getting the first-off part right.”
Previously it may have been the case
that between 10 and 20 parts had to be
produced before consistent production
was achieved. Now they are guaranteed
that the second part off the machine
will be exactly to drawing. The saving
in material and time is significant. This
speed and consistency of set-up fits well
with Duright’s ‘just-in-time’ production
mentality and with batch sizes varying
from 20-off to 1,000-off efficiency in
setting the machines is a valuable asset.
An additional benefit to Duright was
eliminating the need for hydraulic
systems for bending. This has taken
away the risk of oil leaks and the need for
a pump to be constantly running, which
in turn leads to a better and safer working
environment. Electric operation also
gives greater control over the bending
process.
Another factor in the success of the
tube benders is the machine control
and software system, which provides a
seamless crossover between programs
for the tube laser machines and the
Elect benders. The control also provides
detailed feedback to Duright.
“Speed is key when it comes to
quoting, but those quotations need to be
accurate. To achieve speed and accuracy
we invested in a multi-user licence for
the BLM software and we gave all of
our salesmen training in the application
of it. So when a customer sends us a
CAD 3D model (STEP or IGES) our
salesmen can upload it to the software,
which then analyses every option to
bend that tube, whether it’s multi-stack,
one centreline radius, multiple centreline
radii, or variable radius bending, the
software confirms if the bend is possible
and outputs a reliable cycle time, which
leads to an accurate quotation being
produced.”
BLM Group UK Ltd
– UK
Email:
sales@blmgroup.uk.comWebsite:
www.blmgroup.uk.comDuright Engineering
– UK
Website:
www.duright.co.ukThe efficiency of the Elect machines comes
into its own on smaller batch sizes
The powerful Elect 130 is capable of bending
round tube up to 130mm diameter and the
equivalent square or rectangular sections
Duright team leader Daniel Ward (left) with
engineering manager David Wright at the
controls of the Elect 130