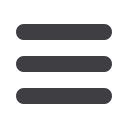

T E CHNOLOG Y
90
SEPTEMBER 2017
The GMAW automated pipe spool welding
solution – Rotoweld
THE Rotoweld is a fully automated pipe
welding work cell developed specifically
for industrial pipe prefabrication, small
pressure vessel manufacturing or
similar 1G welding projects. It integrates
machine vision, adaptive control and
robotics technology in a complete
dedicated solution that is fast and offers
full penetration 1G high quality welding.
Because of the adaptive controls it
welds the open root automatically, in a
normal set-up situation. There is always
some degree of variation in gap and land
and there is also some misalignment
of the wall. This is no problem for the
Rotoweld. Its ‘welder’s’ eye (machine
vision) checks penetration and its
‘welder’s brain’ (adaptive controls) reacts
and adjusts parameters as required to
obtain a good penetration all around. Fills
and caps are welded with fixed settings.
This system is up to five times faster
than SMAW and uses GMAW for the
root, the hot pass and the cap. The work
cell can process spools from 4" to 42". It
can weld pipe to fitting connections and
welds carbon steel pipes with standard
wall at one dia-inch per minute, root, fill
and cap included.
The Rotoweld can weld 12" carbon
steel pipe with standard wall in only 12
minutes, for example. The Rotoweld 3.0
welds the root with GMAW and the fill
and the cap with GMAW, FCAW or SAW.
The Rotoweld is also easy to operate:
at full swing one operator controls the
welding and one operator the unloading
and loading of pipe-spools. A capacity of
300 dia-inch per shift is possible.
The Rotoweld is also of a modular
build. The user has the option to choose
to work with a single bay or twin bay.
However, the twin bay system has major
advantages and is currently the most
popular set-up. The twin bay is the most
efficient choice because of the ability to
work on two bays at the same time and
the higher output this leads to.
The vision-based technology enables
the operator to control the process from
start to finish. The system continually
analyses the image of the root weld pool
picked up by a video camera incorporated
in the welding arm. Unique algorithms
use this information to adjust welding
parameters such as travel speed, wire
feed rate, arc voltage and weaving
width, constantly adapting the process
to varying conditions such as changes in
gap, alignment, root face or temperature.
Full-penetration root pass in an open
bevel joint represents the ultimate in
pipe welding skills and this applies in the
fabrication of pipe spools; that is, a sub-
assembly of pipes and fittings welded
in pipe shops and then sent into the
field. If the welder deposits metal too far
above the weld pool, it sinks and cools
prematurely, so fusion is incomplete. But
if the welder keeps the arc in front of the
weld pool, and at just the right height, hot
metal flows toward the root and a full-
penetration root pass is obtained.
At the Schweissen & Schneiden
exhibition in September, Copier will
exhibit the Rotoweld and would be happy
to welcome visitors to stand 10B04.
In 2014 the company released the third
iteration of the Rotoweld 3.0 technology,
which uses a custom robot to perform 1G
girth welds. The robot arm performs the
root, fill and cap passes with one welding
gun and can be configured for multiple
processes.
For example, a thick walled pipe might
call for GMAW for the root pass and SAW
for the fill and cap passes.
Copier Bevelmachines
–
The Netherlands
Email:
info@copierbv.comWebsite:
www.bevelmachines.comRotoweld 3.0 (twin bay) automated pipe spool welding machine