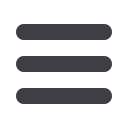

8
Mechanical Technology — July 2015
⎪
Special report
⎪
O
n May 28, 2015 at its East
London plant, having pro-
duced its one-millionth Mer-
cedes-Benz passenger car, a
white right-hand drive C200 Mercedes-
Benz C-Class, MBSA added a milestone
to its journey as an automotive manu-
facturer of premium brand vehicles. The
millionth vehicle was produced following
a complete overhaul of the manufacturing
plant – a R5-billion investment between
2011 and 2015 mooted to be the
largest single-project investment in the
automotive industry in recent history – to
accommodate mostly export demand for
the new W205 C-Class.
The first Mercedes-Benz passenger
car, a W121 Nap Vista Blue Mercedes-
Benz 190, came off the line of the then
Car Distributors Assembly (CDA) plant
in East London more than 57 years ago.
CDA, the company that would become
Mercedes-Benz South Africa, opened
From the first W121 Mercedes-Benz 190 built at the Mercedes Benz South Africa’s (MBSA’s) East London
plant on January 31, 1958, to the fourth generation W205 C-Class – 2015 World Car of the Year – South
Africa’s premium automotive manufacturer has now produced its millionth car.
MechTech
visits the multi-award
winning manufacturing plant.
P
ainting of completed car bodies
manufactured in the body shop is a
vital step in ensuring product quality
for the finished vehicle. The quality of the
applied coating is directly responsible for
long-term corrosion protection and vehicle
life. The paint shop is, therefore, a tightly
controlled area that must remain dust free
and under humidity control.
Following manufacture, the built bodies
with mating doors are transported to the
paint shop on conveyors. Each body has
it own transponder with unique informa-
tion about the finished car’s specifications,
including its future colour.
At the paint shop, bodies are transferred
onto skids, which first guide them though
the pre-treatment process.
Pre-treatment:
Each vehicle body is
washed to remove small particles, grit
and obvious debris. Then the whole body
is immersed and degreased in a chemical
Mercedes-Benz South Africa CEO and executive director for manufacturing, Arno van der Merwe, poses
alongside the millionth Mercedes Benz to be manufactured at the company’s East London plant.
MBSA’s new paint shop for the W205
solvent bath before being rinsed with de-
ionised water. They then enter a chemical
dip tank, where the entire body is sub-
merged so that all crevices can receive
chemical treatment.
The whole structure is then electro-coat-
ed. This is an electrolysis-based process,
also called e-coating or electrophoretic lac-
quering, and provides a chemically-bonded
primer layer onto the entire car body. The
electro-coated car bodies then enter a bak-
ing oven to cure the e-primed layer. This
completes the pre-treatment process.
Sealing and masking:
Prior to painting,
areas that will later have adhesives applied
are masked off. The line of bodies is then
conveyed down to the sealant deck, where
all exposed seams have sealant applied to
guard against water ingress and corrosion.
The underside of the body is sealed using
robot applicators, while at critical points,
sealant is applied and spread manually
by operators. The paint line then passes
through a sealer curing oven.
Painting:
Each vehicle receives three coats
of paint, starting with an inspection stage
where any visible defects are removed. The
bodies are moved through an automatic
cleaning station to remove any small dust
particles.
Primer paint is then applied to act as fill-
ing and smoothing agents. The interiors are
manually spray-painted, while all exterior
Mercedes-Benz: from one to one million