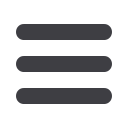

46
S
eptember
2016
USA
BRAZIL
NORWAY
DENMARK
SWEDEN
SPAIN
UK
RUSSIA
FINLAND
ITALY
POLAND
ROMANIA
GERMANY
FRANCE
AUSTRIA
JAPAN
INDIA
MALAYSIA
THAILAND
CHINA
Proven solutions
for the tube and pipe industry
EFD Induction is your worldwide induction partner
with the most comprehensive range of solutions for
the tube and pipe industry:
PUTTING THE SMARTER
HEAT TO SMARTER USE
• Longitudinal seam welding and seam normalizing of tubes
and pipes
• Full body annealing of both magnetic and non-magnetic
tube products
• Tube scarfing systems, coils, impeders and ferrites
• Brazing of heat transfer tubing (boiler, refrigerator and HVAC)
• Preheating and stress relieving
of OCTG pipe ends
• Coating and post-weld heat
treatment (PWHT) of oil and gas
pipes
• Customized solutions for every
dimension and alloy type
EFD Induction
Worldwide
VISIT US AT EUROBLECH
Hall 16, Stand C33
www.efd-induction.comT E CHNOLOG Y
Multi-stage
automated lapping
machine
SUNNEN’S new SVL-
2115 automated lapping
machine claims to bring
increased productivity and
part consistency to what
is traditionally a manual
process.
Based on the same
machine platform as the
SV-2100 honing system,
the SVL-2115 provides
single set-up processing
of
hydraulic
valves,
sleeves, fuel system
components and other
parts that are prone to
distortion when honed. The walkaway system uses an index
table to automatically lap and air gauge bores throughout the
cycle. Gauge readings are fed back to the control and the
cycle is repeated until the parts are within spec.
“Automated lapping is more consistent than manual
and there are fewer workers with the skills necessary for
precision manual lapping,” said Sunnen product manager
Phil Hanna.
“For very expensive parts an automatic lapping process
reduces the possibility of ruined parts due to human error.
Since lapping is usually the last process during the machining
of a workpiece, if the lapping is not correct all the work to get
the part produced up to that point is wasted.”
The Sunnen lapping system handles workpiece diameters
from 6.5 to 20mm (0.26" to 0.7") and lengths up to 12 times
the bore diameter, not to exceed 200mm (7.87").
Spindle speed range is 100-2,000rpm during lapping, but
slow speeds are possible for non-powered steps such as
lapping paste application or slow-rotation bore entry. Stroker
speed is 0-350 SPM, with stroke length optimised to achieve
a high degree of cylindricity.
“This system is a time-saver and it frees operators to run
another machine, or handle other job floor duties,” added
Mr Hanna. “Operators load the workpiece into the fixture and
start the lapping cycle; the cycle ends when the part is in
tolerance.”
Sunnen has developed laps and gauge probes to
accompany the new system, and easy tooling and probe
changeovers accommodate frequent changes during the
course of a shift.
A stack light allows operators to monitor cycle completions
or faults from a distance, while a light curtain is standard. The
lapping system is available with Sunnen’s new SVF filtration
system.
Sunnen Products Company
– USA
Email:
sales@sunnen.comWebsite:
www.sunnen.comSunnen’s SVL-2115