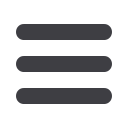

70
S
eptember
2016
T E CHNOLOG Y
IMS Messsysteme GmbH
| Dieselstraße 55 | 42579 Heiligenhaus | Germany
phone: +49 2056 975-0, fax: -140 |
info@ims-gmbh.de|
www.ims-gmbh.deÚ
More Information:
www.ims-gmbh.deE1 | C33
Tube China,
Shanghai
26.–29.09.2016
3700+
Measuring Systems in Use Worldwide
650+
Customers in
60+
Countries
IMS – World Market Leader
in Measuring Systems
10 of the 10 Biggest Tube Manufacturers Trust in IMS
Cutting edge, automated pipe galvanising plant
By Ermes Moroni, general manager and founder, Gimeco Impianti Srl, Italy
HOW do you keep your industrial cost
down and ensure that your quality
standard is up to par with the strict
requirements of today’s market? Very
often, there is one simple answer to
this question: automation. Traditionally
considered less applicable to general hot
dip galvanising, automation is extremely
proficient in standardised products,
such as pipes. In times of thinner profit
margins, having the whole process under
control, while making sure the final quality
is consistent, has become mandatory.
In 40 years of activity, Gimeco has
established itself as a well-known Italian
engineering and manufacturing company
dedicated to the industry of pipe finishing
and hot dip galvanising.
Gimeco now engineers and delivers
complete lines for pipes finishing: hot dip
galvanising, surface finishing, pickling,
phosphating, straightening, chamfering
and threading.
Pipe bundles up to five tons each
are automatically transported through
the process with overhead cranes, fully
controlled by dedicated software.
Gimeco’s plants also feature full au-
tomatic chemical pre-treatment, con-
sisting of an entirely segregated tunnel
enclosure to control the acid vapour
diffusion. While this ensures protection
for workers, it also protects the building
and crane equipment. On top of that,
automatic “recipes” can differentiate
chemical pre-treatment times, adjusting
to variable features of different pipes.
Stats on chemical consumption are
also quickly summarised by dedicated
software functions. As an additional op-
tion to waste management optimisation,
Gimeco supplies a spent acid full
regeneration system to convert the by-
product into useful fertiliser.
A similar approach to energy and
waste efficiency is taken in the high
efficiency infrared drier, which pre-heats
the pipes before entering into the liquid
zinc. Infrared is combined with heat
recovery from the galvanising furnace,
visualising the overall energy balance
with a dedicated tool in the software suite.
Fine control over process parameters
becomes a key to quality and profitability
in the galvanising bath. A dipping system
with vertical screws is coupled with
automatic single or twin pipe pick-up
hooks, offering a good degree of freedom
in tuning key factors. Pipes are forced to
immerse, slowly rotating for better coating
and draining. The first-in-first-out system
is the best way to determine exact time
of transit in zinc, so that given a certain
product diameter or surface quality, each
pipe will be absolutely consistent in final
finish.
An outside zinc wiping system
and inside zinc blowing system with
protruding mandrel and flying nozzle
offer very high surface quality and very
low noise impact.
Gimeco Impianti Srl
– Italy
Email:
info@gimeco.itWebsite:
www.gimeco.com