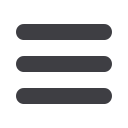

T
ube &
P
ipe
W
elding:
T
rends &
P
rogress
109
M
ay
2008
www.read-tpt.com›
shielding and the argon is being dispersed
evenly over the part, a uniform colour will
be seen. Protective gas flow is still needed
until the metal has cooled below about
250°C, to prevent discolouration.
All work areas must be thoroughly cleaned
according to recommended procedures that
are widely available. All work components
should be considered for cleaning,
depending upon the welding method. For
example, any titanium filler rod material
should be checked for cleanliness.
The welding tungsten should be clean
and new, and not be contaminated by the
welding of other materials on previous work.
Welding torches will occasionally have
leaks that will draw in atmospheric gases
to the shielding gas, so should be leak
tested prior to use. The welded joint must
be allowed to cool before gas coverage is
removed.
Speciality products are now available to
provide quality gas coverage, particularly
low cost flexible enclosures for smaller
components, weld purge monitors and
trailing shields. In addition, there are ‘clean’
expandable stoppers available for use in
sealing tubular components during purging.
Flexible welding enclosures are lower
cost than the more traditional solid metal
versions. Additional benefits include
the flexibility of minimal weight and the
relatively fast times to achieve a weld
purge. Flexible enclosures are sometimes
not robust enough for welding operations.
However, they are made of tough PVC
plastic, and the cold purging gas helps to
quickly dissipate the welding heat.
Early flexible enclosures were circular in
section, but are now available in square
and rectangular shapes. Coupled with
the ability to produce lengths to order,
rectangular cross sections have made the
new additions attractive to a wider range of
end-users. Such enclosures are available
up to 2m long and 1m x 1m in section.
There are now low cost instruments
designed specifically for weld purging,
measuring oxygen levels in any purge gas
during the welding of titanium and its alloys.
They show oxygen levels down to 10ppm
using an alphanumeric display. Features
include automatic fault finding diagnostics
and data acquisition software.
Devices called ‘trailing shields’ are
available, and will fit any make of GTAW
(TIG) or PAW (plasma) welding torch.
They are available in flat format for sheet
metal welding and in radiused format to
match any diameter of pipe or vessel. The
radiused versions are manufactured for
welding on inside radii as well as outside.
For mechanised welding machines, where
weight and size considerations are less
constraining, the trailing shields are larger,
giving greater gas coverage and faster
welding.
In recognition of the cleanliness required for
reactive metal welding, clinically prepared
expandable plugs are also available and
widely used to seal pipes so that good
gas coverage is maintained. Such plugs
are available from 12 to 160mm (0.5 to 6″)
diameter.
This article was prepared by Dr Mike Fletcher and
Ron Sewell
References:
1. Recommended practices for gas tungsten arc
welding of titanium pipe and tubing (American Welding
Society – NSI/AWS D10.6/D10.6M:2000)
2. Specification for fusion welding for aerospace
applications (American Welding Society – ANSI/AWS
D17.1:2001)
3. Guide for the fusion welding of titanium and titanium
alloys (American Welding Society – ANSI/AWS G2.4/
G2.4M:2007)
Huntingdon Fusion Techniques Ltd
– UK
Fax
: +44 1554 836837
:
rasewell@huntingdonfusion.comWebsite
:
www.huntingdonfusion.com
Trailing shields for Tig/GTAW welding of titanium
Outstanding Tube Mill Cutoff Systems and Tooling
New-Variable
Speed Shear
Improves
Performance
Nick ‘N’ Shear
®
Dimple Free Tooling
Single Cut Die Sets
Die Jaws
Blades
Outstanding Tube Mill Cutoff Systems
P.O. Box 334 • Troy, Michigan 48099 USA
Voice 248-853-0446 • Fax 248-853-6353
E-mail:
brsales@betaram.com•
www.betaram.com