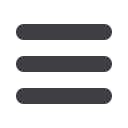

news
Wire & Cable ASIA – May/June 2008
38
Ultrasonic welding and bonding
tecchnology specialist Sonobond
Ultrasonics has announced that
increasing numbers of companies are
relying on its microprocessor-controlled
spot welding technology.
According to Janet Devine, the
company’s president, manufacturers
are reporting that the SonoWeld
®
1600
digital metal spot welder series is
proving to be dependable, efficient,
and easy-to-operate, citing Lake Cable,
LLC as an example of a company that
is obtaining impressive results from the
technology. The company encapsulates
cables in metal sheathing and extrudes
overall jackets over its control,
instrumentation, and power cable
product line.
Lake Cable needed to update its spot
welding machine at its 100,000ft
2
Prairie
Cable facility in Valparaiso, Indiana.
According to that facility’s maintenance
manager, Chris McLaughlin, they were
already familiar with many of the
advantages of Sonobond technology.
“We had been using a 20 year old
Sonobond machine and were very
pleased. We knew there were other
assembly methods but, unlike
ultrasonics, these other methods were
less efficient and used consumables.
We didn’t want that. When we
contacted Sonobond to replace a
manual we’d lost, they recognised that
a newer, customised unit could help us
improve our existing processes.”
Sonobond responded promptly by
providing free sample welds and a
recommendation that Lake Cable, LLC
replace the current unit with a specially
modified version of the 2500-watt
SonoWeld 1600 digital metal spot
welder. This new unit featured a custom
anvil slide assembly, as well as a
modified frame to accommodate
material up to 4.5" in width. It also
enabled the unit to weld on an angle so
that the stress would be spread out to
make a stronger joint.
As a result, it was found that the weld
strengths of the new joint equalled
90% of parent material strength, and a
¾" weld took only ½ second.
Other features that make the SonoWeld
1600 popular with manufacturers
include a power supply with built-in
microprocessor to permit storage and
recall of over 250 weld protocols. The
easy-to-operate unit also features
automatic frequency control, overload
protection and automatic quality
monitoring. The efficient metal spot
welder has heat-treated, tool steel
taper lock tips that can perform up to
300,000 welds before being replaced.
A digital display allows selection of
welding modes by time, energy or final
weld thickness.
In ultrasonic welding, high frequency
ultrasonic energy is directed via a
welding tip to the surfaces for the
metals to be welded. The energy
disperses the oxides and surface films
between the work pieces to create a
true metallurgical bond without melting
the materials. Ultrasonic welding is
environmentally friendly, produces no
waste, and is economical. The patented
Wedge-Reed coupling system assures
precise, dependable welds and can be
mounted in a variety of orientations for
special applications.
Sonobond Ultrasonics – USA
Fax:
+1 610 692 0674
Email:
info@sonobondultrasonics.comWebsite:
www.sonobondultrasonics.comSonobond Ultrasonics’ spot welding technology