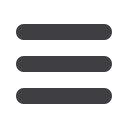

January 2015
32
www.read-eurowire.comNews
Technology
Cold pressure welding offers wire
and cable manufacturers a quick and
cost-effective method of permanently
joining non-ferrous materials and their
alloys without heat, flux or fillers.
The process offers many benefits: it
produces permanent welds stronger than
the parent material, while the electrical
integrity of the material is not affected.
It can be used to join strip and profile
as well as round wire; even dissimilar
materials and materials of two different
sizes can be cold-welded.
Because cold welding takes place at
ambient
temperatures,
no
thermal
changes occur in the material being
welded, so there is no splattering or
waste, and no risk of the operator being
burned.
Welding with cold pressure is also
simple and inexpensive. Fine wire can be
joined in seconds using small, manually
operated cold welders. Powered machines
are required to weld larger wire and rod
sizes, but use considerably less power and
take much less time than electrical butt
welders.
The cold weld process employs a
‘multi-upset’ technique, whereby the
two ends of the material are gripped and
forced together under high pressure.
Each time the cold welding machine is
activated, the material is gripped by the
die and fed forward.
As the two ends of the material are
pushed against each other, they are
stretched and enlarged over their entire
surface area. Oxides and other surface
impurities are forced out and a bond
is formed. A minimum of four upsets is
recommended to ensure all impurities are
squeezed out of the interfaces.
The design of the dies is crucial – they
must hold the material firmly to avoid
slippage. To improve the grip, the inside
of the cavity is either etched with an
electric pencil, or, when the die is to
be used for joining large pieces of
aluminium, grip marks are put in the
cavity before the die is heat treated.
The gap between the two faces or noses
of the die is particularly important. If it is
too large, the material will just collapse
or bend away. This dimension is carefully
calculated during die manufacture and
cannot be changed.
Lastly, there is the offset of the die noses.
This has the effect of making the weld
look out of line around the circumference
of the material. The purpose of the offset
is to break the weld flash or burr (spare
material containing impurities which is
pushed out from the core of the weld)
into two halves to allow it to be removed
easily.
PWM (PressureWelding Machines) Ltd
– UK
Website
:
www.pwmltd.co.ukEffective welding with cold pressure
▲
▲
The EP500 rod welder from PWM