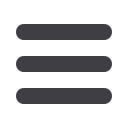

Technology
Update
29
J
uly
/A
ugust
2007
Wanzl’s production director and company
secretary
.
Following the installation of a LT712D, which
is equipped with a 2kW laser and is some 30
per cent more productive than the LT652,
Wanzl began working a three-shift
system with the two computer-
controlled machines supervised
on each shift by one operator.
“The level of finish quality from the
welding of the tube has only been
made possible by laser cutting,”
explains Mr Boxler
, “We quickly
began to favour laser cutting
when designing our products and
this has produced savings on
component wastage, on welding
and, importantly, on the number
of parts requiring rework – plus a
massive improvement in quality.
In other words, the tubes are
more accurate and repeatable,
so the manufacturing path has
become simpler and more
rational. This has allowed us to
make some of our products in kit
form for self-assembly.”
In recent times Wanzl has assembled
a team of laser cutting specialists and
technicians, who are extremely enthusiastic
and highly motivated.
“When we discuss new products ‘laser
man’ is always around the table,”
says Mr
Boxler,
“identifying opportunities for the
most effective methods of production, right
up until the end of the project.”
“We cut up to 440,000 tubes and profiles a
year in batches from 1 to 500 pieces and
we have never had any problems with
the aluminium and stainless steel we are
cutting. This has helped Wanzl to implement
just-in-time production and to reduce stock
and work-in-progress to a minimum.”
BLM Group UK Ltd
– UK
Fax
: +44 1525 402 312
:
sales@blmgroup.uk.comWebsite
:
www.blmgroup.uk.comWanzl Metallwarenfabrik GmbH
– Germany
Fax
: +49 8221 729 100
:
info@wanzl.deWebsite
:
www.wanzl.comLoading/unloading with 180° part rotation capability
Toellner Systems, USA, has announced a breakthrough in new technology for
automated part loading and unloading. The company is a leader in automated loading/
unloading of CNC lathes,
machining
centres,
grinders, shaft cut-off,
multi-spindle chuckers,
and thread rolling.
The new technology can
rotate selected parts
180° and reload them
for Op 20 machining.
When combined with this
technology, load rates as
low as 5 seconds provides
immediate
throughput
increases of up to 50 per
cent.
Materials such as steel,
aluminium, cast iron, forgings, titanium, powdered metal, brass, copper, plastics,
graphite, composites, ceramic, rubber, wood, and most metals can be easily adapted to
these systems.
The machine is capable of handling a variety of shapes and lengths. The part loading
system can be easily adapted to production machines.
Toellner Systems Inc
– USA
Fax
: +1 715 424 4527
:
info@toellner.com•
Website
:
www.toellner.com›
Part loading and unloading technology with 180º part rotation
fi
Shopping in style – BLM laser cutting systems are an integral
part of Wanzl’s shopping trolley production process
Laser cutting systems boost
shopping trolley production
Following the installation of a BLM LT712D
laser tube cutting system, shopping-
trolley manufacturer Wanzl have reported
a substantial increase in productivity.
Established in 1918, Wanzl is a leading
producer of supermarket shopping trolleys
and has a daily output of over 7,000 trolleys,
manufactured at its facilities in Kirchheim,
Germany. The trolleys are manufactured
from around 7.5 million metres of tube a
year.
The company also manufactures significant
numbers of luggage trolleys, and in 2003
supplied 11,000 to Charles de Gaulle airport
in Paris, the largest order ever placed by
an international airport. Wanzl operates
two manufacturing facilities in Germany
(Leipheim and Kirchheim), where it has
gained great benefits from the incorporation
of BLM Adige laser tube cutting systems
into its production process.
Wanzl installed the first BLM Adige
laser cutting system five years ago at
its Kirchheim factory. According to the
company, this LT652 system paid for itself
within two years and in December 2005
a second BLM Adige laser tube cutting
system came on stream.
“We have never had any problems with our
laser machines as we spend time doing
necessary
preventative
maintenance.
Given that we are working to full capacity,
it is important to maintain a high level of
machine efficiency,”
says Mr Anton Boxler,