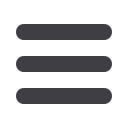

S
traightening &
F
inishing
T
echnology
74
J
uly
/A
ugust
2007
After the introduction of high-speed CNC
tube bending machines the demands of the
industry changed. Furniture makers now
demanded very good straightness so that
the loading and feeding stations could feed
the tube into the CNC bender at high speed
and without any misfeed or tube jams.
Although 6-roll straightening machines
have their niche, today, the 10-roll machine
is now the standard. Automotive prop
shaft tubing, steel or aluminium is the
preserve of the 10-roll, computer controlled
straightening machine. With 5 pairs of
vertically opposed rolls, the outgoing
tube is corrected to less than 0.001" TIR
(0.025mm) with exacting straightness.
The difficulty in setting 10-roll machines
initiated the development of computer
setting systems in the late 1980s. These
systems store all the required data to reset
the machine for a specific tube.
This stored data is used to control
motorised roll positioning equipment to
reset the machine for a new size of tube in
less than a minute. The majority of 6 and 10
roll machines are now shipped
with these systems.
Computer setting systems
provide more accurate roll
positioning and ensure that
each operator sets the machine
with recorded and well-
established roll positions.
Tube quality is maintained from
batch to batch due to setting the
rolls to the same positions that
were used to run the machine
when that specific tube size
was last produced.
Small batch production with many size
changes per shift is now possible with
consistent quality. In addition to providing
better tube straightness and ovality, the
10-roll machine produces a considerable
increase in straightening consistency.
This increase in consistency is clear when
processing badly bent tubes. It is a function
of the additional number of plastic cyclic
deflections that occur within this type of
machine.
The 10-roll machine is clearly more flexible,
being able to apply a large bending moment
at the first pair of deflecting rolls, which is
then linearly reduced to apply a finishing
action at the last pair of deflecting rolls.
The leading end and trailing tube ends are
straightened more effectively due to the
ability of the machine to apply additional
pressure straightening between 5 pairs (10
roll) rather than 3 pairs (6 roll) of rolls.
Turner Machine Company Inc
– USA
Fax
: +1 330 332 5871
:
turnermachine@turnermachineco.comWebsite
:
www.turnermachineco.comfi
Computer setting systems ensure more accurate roll positioning
88