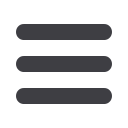
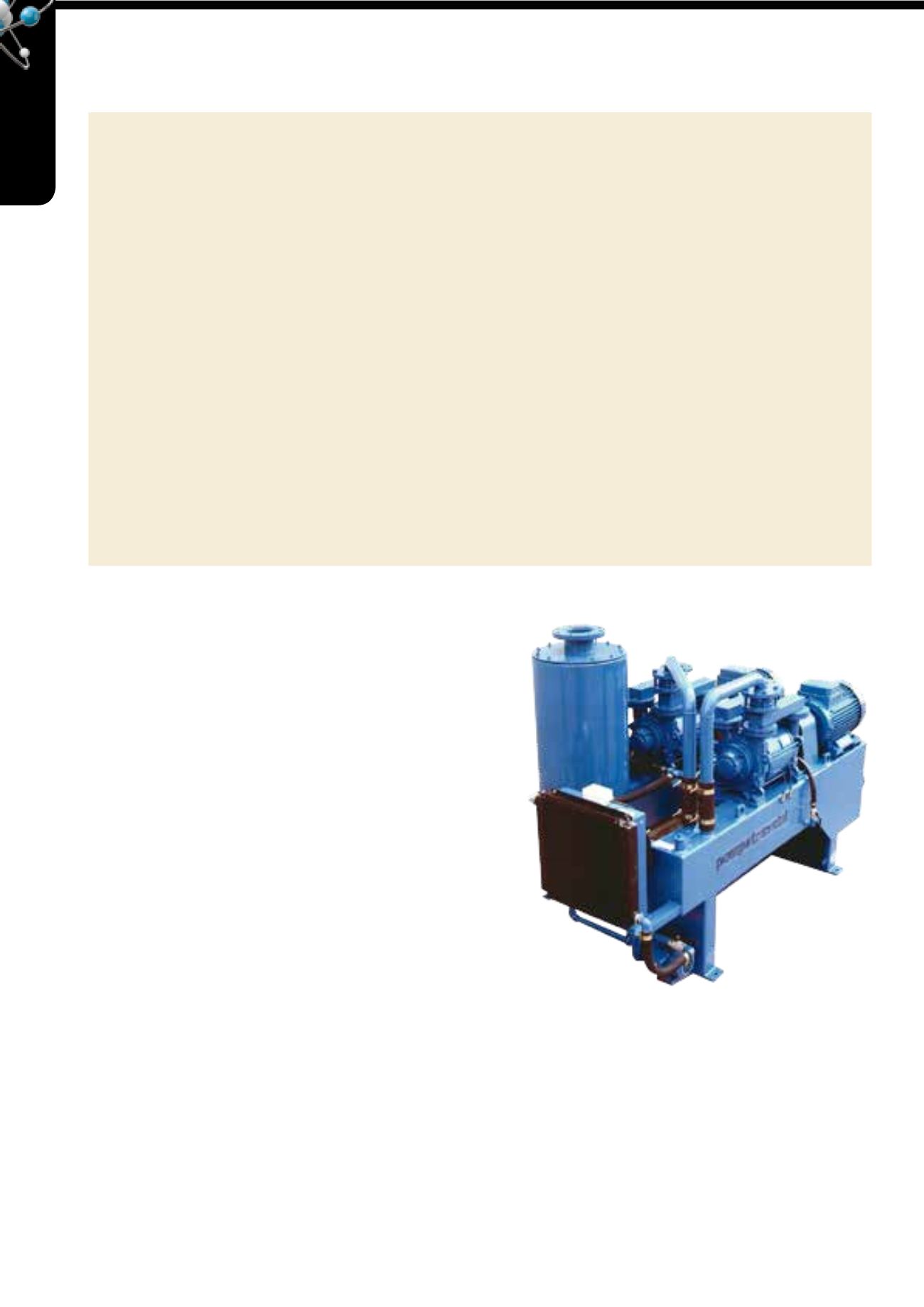
Outotec modular plug-and-play solution for industrial water treatment
In order to be more environmentally
sustainable, the mining and mineral
processing industry is focusing more on
ways to minimise impact on the surround-
ing environment. Outotec has combined
its particular understanding of water
treatment, process design, electrolysis
and hydrometallurgy into a cost-effective
modular product called Outotec®EWT-40.
The Electrochemical Water Treatment
process solution is a highly automated
process, which minimises the need for
personnel while ensuring high quality
water treatment performance.
These EWT solutionsmay be purchased
as a process solution island with full
maintenance, spare parts and operational
support services. Outotec can also offer a
complete water treatment solution from
test work including: laboratory scale test
work to on-site piloting, conceptual and
feasibility studies, basic and detailed en-
gineering, as well as developing a solution
for the entire process.
Potential sources of water contami-
nation from the mining industry include
drainage from surface and underground
mines, wastewaters from beneficiation,
surface run-off and acid mine drainage
(AMD).
Outotec Electrochemical Water Treat-
ment solutions can handle everything
from the removal of arsenic, selenium
and antimony, to trace metals and organic
removal. Customer specific wastewater
can also be tested in Outotec’s lab in
Pori, Finland.
One Outotec EWT-40 module can treat
approximately 5-40 m³/h of wastewater
depending on the application. The opera-
tion can easily be scaled up as needed
simply by adding more modules.
Another benefit of its modular design
is the added value it brings to customers;
the modules can be easily relocated or
resold, protecting the investment beyond
plant lifetime. It is also ideal for remote
locations with minimum transport and
storage needs.
• Fast, efficient water treatment and
lower residual impurities compared to
conventional processes
• Modular design supports easy reloca-
tion and expansion
• Highly automated process minimises
personnel requirements and enables
remote operation and monitoring
• No need to procure or handle
chemicals.
For more information
go to:
www.outotec.comFOCUS ON WASTE
MANAGEMENT
Pompetravaini SpA was founded in 1929
by the late Carlo Travaini, an experienced
machinist with solid production experience
acquired while working at the company
Franco Tosi of Legnano, Italy.
He started his own business under the
name of Travaini Mechanical Machining,
producing many different types of pumps
under private labels with designs and
materials supplied by customers. In the
following years, the ever growing experi-
ence and continued technological updating
of the manufacturing plant increased the
growth potential forcing a major expansion
of the business.
The current President, Ing Mario Tra-
vaini, decided in 1968, to rename the
company Pompetravaini SpA. With tech-
nologically advanced production and a
sales network adequate for the times, the
company began selling products in the
European market under its own label.
Once more the company outgrew its
facilities and in 1982 a new site of approxi-
mately 8000 m
2
was built in the industrial
area of Castano Primo, Milan (Italy).
Parallel to the internal growth there
has been a marketing expansion into
international markets. In 1985 Premier
Fluid Systems Canada started opera-
tion, followed in 1986 by Travaini Pumps
USA. In 1989 Travaini Pompen BeNeLux
was founded in the Nederlands and two
A brief history of the Pompetravaini Group
The OilSys Doppio
from Pompetravaini, avail-
able from Vactec in South
Africa
years laterr, in 1991, Travaini
Pumpen GmbH in Germany
began operating. In 1999
Pompes Travaini France
started in France.
In 2002 there was an-
other addition to the existing
plant. A building of approxi-
mately 4000 m
2
was added
to house a new computerised
stock room and assembly
room. This futuristic project
utilises LGV (laser guided ve-
hicles) to store components,
bring them to the assembly
area and then bring the as-
sembled pumps to the test
room.
In 2007 Travaini Pompy Polska was
founded and the following year, after 54
years of total dedication and intense ac-
tivity as President, Mario Travaini handed
over to his son Carlo who has been re-
sponsible for the last steps that moved
Pompetravaini into a new era with ‘state
of the art’ automation.
Various new acquisitions have taken
place since 2012, including NSB gas
processing AG and BORA Blowers; and
FuturEng, an engineering office for design
and construction of skids with rotating
equipment, was founded.
Air & Vacuum Technologies have been
the sole agents for the full Travaini range
for almost ten years now and, according to
Mark Burn, managing director, the brand
is growing from strength to strength with
sales figures growing year on year.
For more information contact:
Mark Burn on 0861 VACTEC (822 832)
or tel: +27 11 318 3240-5;
or go to
www.vactech.co.za10
Chemical Technology • June 2016