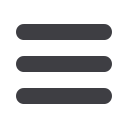

Industry News
www.read-tpt.com10
J
anuary
2014
Bulgarian tube maker
HUS chooses EFD
Induction Weldacs
HUS, the Bulgaria-based steel and
tube maker, has ordered four complete
Weldac induction welding systems from
EFD Induction. The systems will be
installed in HUS’s new manufacturing
facility in the city of Lom in northern
Bulgaria, which has a planned monthly
output of 12,000 metric tons.
“After carefully examining various
suppliers we were finally convinced
by the proven ability of the Weldac to
reduce operating costs while delivering
outstanding throughput,” said HUS
export director Dimitar Milenkov. “Also,
the fact that EFD Induction is present
throughout Europe, including having a
major factory in Romania, means we
have considerable after-sales support
on our doorstep.”
The four Weldac systems ordered by
HUS range in power from 125 to 450kW.
Each welder features impeders from
Electronic Heating Equipment (EHE),
the US impeder specialist acquired by
EFD Induction in 2012. “The inclusion
of the EHE impeders is important,” said
Matthias Gruber, managing director of
EFD Induction Austria, who was one
of the team that secured the order. “It
shows how we can supply complete
induction welding solutions that are
customised to specific customer needs.”
HUS’s new factory in Lom, together
with the four new Weldac welders,
makes the company one of Bulgaria’s
largest tube and pipe companies. “We
already export, particularly to customers
in the Balkans and Eastern Europe,”
said Mr Milenkov. “However, we aim
to export much more to other markets,
especially after our acquisition of
Kloeckner Bulgaria earlier this year. In
fact, all the tube and pipe welded by the
new EFD Induction Weldacs will be sold
to customers in Central and Western
Europe.”
Two of the four Weldacs have already
been shipped to HUS. “The schedule is
for the remaining two to be completed
at an EFD Induction production facility
in Norway and shipped to us by the end
of October,” said Mr Milenkov. “So we’re
very busy preparing our factory and
setting up the lines. I mean, the arrival
of one brand new Weldac is an event,
but four in the space of a few weeks is
certainly a major turning point, not just
for HUS, but for the entire Bulgarian
tube and pipe industry.”
EFD Induction has to date installed
thousands of heating solutions for a
wide range of industrial applications
– bringing the benefits of induction
technology to many of the world’s
leading manufacturing and service
companies.
EFD Induction has manufacturing
plants, workshops and service centres
in the Americas, Europe and Asia.
Corporate headquarters are in Skien,
Norway.
EFD Induction as
– Norway
Website:
www.efd-induction.comBenteler enters North American
seamless tube market
IN the course of implementing its growth
strategy, Germany company Benteler
Stahl/Rohr (BSR) has concluded a
contract with Danieli & C, Italy, for a new
turnkey 4½" seamless tube mill.
The mill will be built in Shreveport,
in the north-western part of Louisiana,
USA, and will be one of the largest
production plants in the history of this
region. The mill is designed for an
annual capacity of 320,000t and will
produce high-quality seamless tubes
with excellent tolerances and material
properties according to API and ASTM
standards.
Within the framework of its cooperation
with Danieli Centro Tube, Friedrich
Kocks GmbH & Co KG will supply an
EXB 315/3 extracting block and an
SRB 315/30 stretch reducing block as
essential components of the hot rolling
mill. BSR opted for rolling blocks with
a modular design, which are equipped
with both non-adjustable and adjustable
roll stands. The stands are operated
with individually driven rolls, which are
interchangeable so they can be used in
the EXB as well as in the SRB on every
stand position.
The specification of this design,
including pass remote control for
the adjustable stands, and quick-
changing systems for stands and
rolls, minimises the number of
changing stands required for optimum
production. The automation system
enables the visualisation of the
measured data of the rolling mill, while
allowing the operator to control the
operation, minimising heavy ends and
wall thickness variation.
Production of the mill is scheduled for
the second half of 2015.
Friedrich Kocks GmbH & Co KG
–
Germany
Fax: +49 2103 512 49
Email:
marketing@kocks.deWebsite:
www.kocks.deDanieli & C
– Italy
Fax: +39 0432 1958289
Email:
info@danieli.itWebsite:
www.danieli.comBenteler Stahl/Rohr
– Germany
Website:
www.benteler.comMr Milenkov signing the EFD order