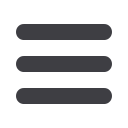

⎪
Pump systems, pipes, valves and seals
⎪
Mechanical Technology — June 2016
15
Harry Rosen:
a UNIDO International Pump Expert
H
arry Rosen, with 25 years of experi-
ence in the pumping industry, is the
managing director of TAS Online, an
international market leader in engineering
software and consulting services for both
users and manufacturers of pumps. The
company’s global service offering includes
pump selection software, pump monitoring
products, on site system assessments and
performance tests, in addition to Testbed
automation systems.
Rosen studied at Wits University and
qualified with a BSc Mech Eng in 1987,
receiving his Pr Eng in 1992. He is a past
chairman of the SA Institution of Mechanical
Engineering, Central Branch and was instru-
mental in setting up the International Pump
User Conference (IPUC), which brought to-
gether the world’s experts in energy efficient
pumping systems.
He has carried out more than 50 pump-
ing system assessments, both in South
Africa and around the world, for applications
including: bulk and municipal water supply;
iron and steel manufacturing; petrochemical
and process plants; mining (underground,
open cast and dune mining) and minerals
processing plants; power stations; pulp and
paper plants; and sugar mills.
Harry Rosen was recently appointed
as one of only two International Pump
Experts for the United Nations Industrial
Development Organisation (UNIDO) deliv-
ering expert pump training programmes in
South Africa, Malaysia, Indonesia, Thailand
and Philippines. He has also been involved
in the UNIDO ‘Train the Trainer’ programme,
whereby a group of pump experts is selected
to be developed as pump systems efficiency
trainers.
He also presents a three-day workshop
for 2KG Training on improving the efficiency
and reliability of pumping systems. This
workshop is CPD approved and has been
supported by Eskom and the National Energy
Efficiency Agency as a valuable tool for
helping industry achieve its targeted 15%
savings in electricity.
q
Figure 2: Plant operators found that if they left the vent pipes open during normal pumping operation, the
stream of water back into the hot well was a visible means of identifying any loss of priming.
for process cooling.
The level of the water in the sump is
below the intakes of the pumps, which
can cause ongoing problems for the
pumps due to loss of priming and suc-
tion lift. Vent pipes had been installed on
the discharge of the pumps to facilitate
the removal of air from the system when
priming the pumps. Plant operators
found that if they left these pipes open
during normal pumping operation, the
stream of water back into the hot well
was a visible means of identifying any
loss of priming and thus avoiding cavi-
tation and the pumps running dry (See
Figure 2).
The opportunity:
Adopting the systems
approach above, these vent lines are
functioning similar to a permanently
open bypass line, meaning the energy
consumed to pump this portion of the
flow is wasted. The flow was measured
to be in the region of 3.0% of pump flow,
which superficially does not seem a lot.
However this translates to between 3.0
and 5.0 kW per pump – and in a single
pump house operating with three hot-
well pumps of 160 kW each and three
cold-well pumps of 100 kW each, the
total power loss comes to 25 kW, or
197 000 kWh of wasted energy per year.
The Philippines currently has the second
highest cost of power in Asia (Japan has
the highest) and at 10 Pesos per kWh,
this ‘waste’ amounts to 1.97-million
Pesos (R630 000).
In addition, there were at least anoth-
er 14 pumps in the plant operating with
open-vent pipes, causing total energy
wastage of around 410 000 kWh costing
P4.1-million (R1.3-milion).
During a pump performance test, we
found that the flow rate through Pump #3
was dramatically down, and the pump ef-
ficiency was as low as 30%. Even though
the vent line was full, the pump had not
been primed correctly and had been
operating in that condition for more than
24 hrs, wasting excess energy as well
as systematically destroying the insides
of the pump. This proved that observing
a stream of water through the vent line
was ineffective in determining whether
the pump was primed correctly or not.
The proposal
Proposed options for rectifying the prob-
lem include:
• Install cheap pressure gauges on the
suction of each pump to identify any
loss of priming as well as the onset of
cavitation. By alerting operators to any
suction issues and remedying them,
energy consumed is reduced and the
reliability and life of the pumps is
extended.
• Only open the vent (bleed) lines when
priming the pump, to get rid of any air
in the system. The rest of the time the
valves should be closed.
• Use the energy savings from the
above project to invest back into more
capital-intensive projects, and save
even more energy.
In my next column, I will look at the is-
sue of throttling losses through control
valves.
q