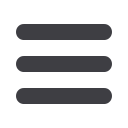

34
M
arch
2015
Technology News
Omni-x end forming tools
ALTHOUGH mainly known for the
design and production of tube bending
tooling, Omni-x has now become a large
producer of end forming tools.
The decision was made following
significant demand from its customers
to not only produce tooling for tube
bending machines but to also produce
tools for their end forming machines.
It was decided to invest in new
machinery and into the design process.
“We wanted to ensure that the quality
and performance of our end forming
tooling was to the same standard as our
tube bending tooling,” said Omni-x MD
Josef Weber.
“The response from our customers
has been very encouraging and the
growth from this part of the business
has been unprecedented. We have the
capacity to produce end forming tooling
for tubes from OD 20mm to 76.2mm.
“There are three variants of end
forming that Omni-x produces – I/O,
C-Reducing and C Expanding. This is a
two-function segmented shaping tool I/O.
It is suitable for reduction and expansion
of tube diameters. Complete assembly
is composed of external collets, internal
fingers, mandrel and barrel in which the
individual parts are assembled.”
This type of tool is the only one that
has fingers and external collets. This
means that it is possible to re-enforce
the shaped area from the inside or
the outside, which gives much greater
variability in this type of tool. From the
range of segmented shaping tools, the
I/O gives the user quality from the point
of view of tube shaping.
The
single-purpose
segmented
shaping tool is marked with a “C” or an
“R” and is used for reducing the diameter
of the tube. The complete set contains
an outer collet, a gripping adapter and
a cone. This type of tool contains only
external collets. This means that it is
possible to put pressure on the shaped
area from the outside, which allows the
user to reduce the diameter of the tube.
The
single-purpose
segmented
shaped tool is marked “C” or “E”. It is
suitable for expanding the tube diameter.
Complete assembly is composed of
internal fingers, mandrel and barrel
in which the individual parts are
assembled. This type of tool contains
only expanding fingers. This means that
it is possible to put pressure the shaped
area from the inside, which allows the
user to expand the diameter of the tube.
Omni-x CZ sro
– Czech Republic
Fax: +420 548 212 804
Email:
sales@omni-x.czWebsite:
www.omni-x.czFrom coil to finished tube
FOUR years ago the owner-managed
Asmag Group from Austria took
over Seuthe in Germany and in that
time both companies have enjoyed
considerable success both individually
and as a one-stop equipment supplier
for tube mills.
Asmag, the Austrian machinery and
plant manufacturer for the steel tube
and non-ferrous metal industry, has
achieved premium product quality
and manufacturing productivity in
drawing, straightening, sawing and
cutting, chamfering, stacking and
bundling equipment. The company is
an experienced global supplier whose
innovative products stand out for
efficient productivity and high quality
manufacturing standards. Asmag’s
strengths lie in its depth of in-house
manufacturing capabilities. It offers
effective communication, personal
service and support.
For the last 30 years, companies in the
tube and profile manufacturing industry
have been relying on customised and
individual solutions from Asmag GmbH,
which is based in Scharnstein, Austria.
Whether a customer needs equip-
ment for extrusion, pointing, drawing,
straightening, cutting and chamfering,
finishing, stacking and bundling or
material handling – engineers for special
purpose machinery and plant equipment
will question, scrutinise, investigate,
research, develop and design for as
long it takes to ensure the smallest detail
fits and the best solutions have been
found.
Asmag believes a new system
should not just provide customers with
a flexible, faster and more economical
production solution – it should also bring
with it specific competitive advantages.
The organisation and structure of
Asmag are customer-orientated and
adapted to customer needs. A project
manager acts as a competent partner
for each customer and is responsible
for all processes from the beginning of
a project to start-up at the customer’s
site.
A qualified engineering team and an
experienced production team assure
that exactly the equipment desired is
delivered to the customer. It is the goal
of Asmag to achieve that.
Asmag GmbH
– Austria
Fax: +43 7616 880188
Email:
sales@asmag.atWebsite:
www.asmag.atSeuthe GmbH
– Germany
Fax: +49 2372 506 111
Email:
sales@seuthe.comWebsite:
www.seuthe.comView inside an ASMAG straightener