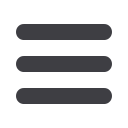

Technology News
www.read-tpt.com70
M
arch
2015
Order for push/pull pickling line
NELSON Steel and Vigano Srl have
been selected to build a push/pull
pickling line for ATS in Poland. Nelson
Steel will be responsible for the process
section, and Vigano is responsible for
the entry and exit equipment on the
line.
Nelson Steel states that its position
as operator/designer and manufacturer
of pickling lines makes it an ideal
choice as a supplier of steel pickling
equipment, with expertise in all aspects
of operations.
The ATS pickling line is specified
for operating at a maximum target
of 200,000 tonnes per year, and at a
maximum line speed of 40mpm. Coil
size is up to 30,000kg at 6 x 1,600mm
maximum width. The process section
equipment consists of three pickling
tanks, each 10m in length; ‘Turbo Tunnel’
design to effectively reduce consumable
cost of acid and gas consumption; acid
recirculation system; a three-stage rinse
spray system; single air blow off system;
fume exhaust system; and ferrous
chloride and raw acid storage tank farm.
While this is a relatively small capacity
pickling line, Nelson Steel describes it
as a good opportunity to create greater
awareness of its brand in Europe.
Nelson Steel owns and operates
pickling lines, and has provided steel
pickling services to the steel industry
for over 35 years. During this time,
the Nelson Steel Technology Group
has designed and built more than 75
complete process sections, including
many revamps. Nelson Steel is a division
of Samuel, Son & Co, Ltd, and is based
in Stoney Creek, Ontario, Canada.
Nelson Steel
– Canada
Email:
sales@nelsonsteel.comWebsite:
www.nelsonsteel.comSamuel, Son & Co Ltd
– Canada
Fax: +1 905 279 9658
Email:
sales@samuel.comWebsite:
www.samuel.comTube
cleaning
THE Compri Tube Clean System
cleans tubes by shooting a special
projectile with a jet of compressed air.
The system can be applied to tubes
with an internal diameter from 2mm up
to a few hundred, and lengths of 10,
100 or even 1,000m (depending on
the air capacity). It can also be applied
in the presence of 90° curves, T or Y
couplings or ball valves.
The system can clean tubes of all
types, from those used in hydraulic
systems, to air conditioners, from the
food industry to pharmaceuticals. It can
quickly and efficiently degrease, lubricate
and disinfect using, when necessary,
minimum quantities of chemical products.
Alka Srl
– Italy
Email:
info@alka-srl.comWebsite:
www.alka-srl.com