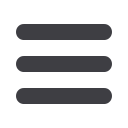
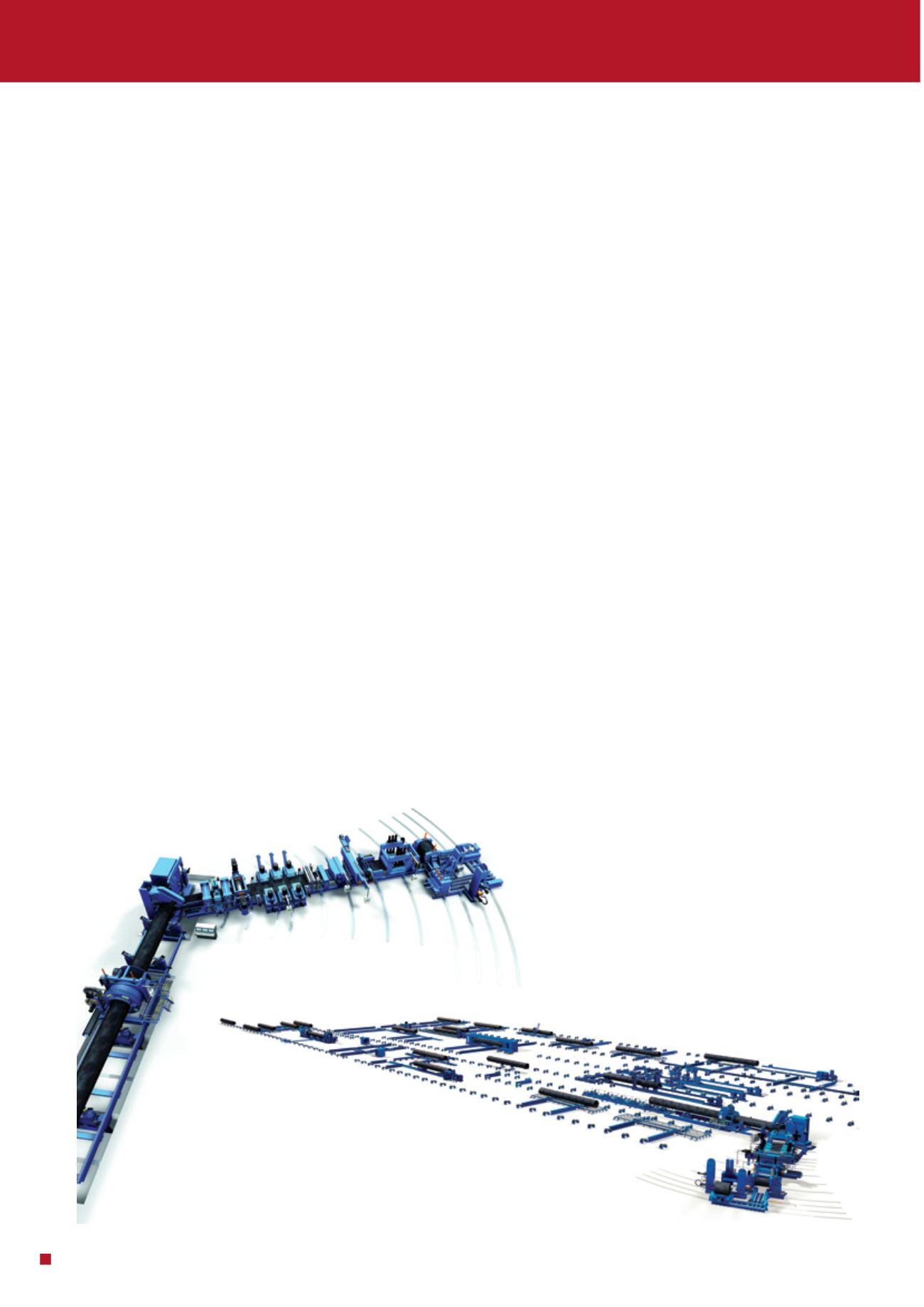
Industry News
www.read-tpt.com6
M
arch
2015
Major order for spiral pipe mill
SCHULER has received a major order
for delivery of a spiral pipe machine, from
a manufacturer of steel pipes in Mexico.
Tuberías Procarsa will use the off-line
machine to produce large pipes with
diameters from 508 to 2,235mm (20" to
88") and lengths from 12 to 24.4m. The
pipes will mainly be used for building
pipelines in oil and gas extraction.
The input stock for the large pipes
is a coil-wound strip up to 25.4mm
(1") thick, comprising high-grade steel
(up to X100). The spiral pipe machine
forms this material into the required pipe
diameter and connects the edges by
tack welding. Welding of the pipe is then
completed on a separate welding stand
using the submerged-arc method.
The pipe mill has a length of more than
450m, and includes various facilities
for testing the large pipes according
to API standards. Ultrasound, X-rays
and pressurised water are used for
this process. The mill from Schuler will
increase Tuberías Procarsa’s production
capacities by 220,000 tonnes per year.
Schuler offers presses, automation
solutions, dies, process technology
and service for the entire metalworking
industry and lightweight automotive
construction.
Clients include car manufacturers and
their suppliers, as well as companies
in the forging, household equipment,
packaging, energy and electrical
industries.
Schuler AG
– Germany
Fax: +49 7161 66907
Website:
www.schulergroup.comRussian producer of API grade
pipe selects Thermatool
ATHERMATOOL three-stage (1,500kW)
seam annealing system has been
selected by one of Russia’s leading
producers of API grade pipe. The latest
Thermatool seam annealing technology
will be delivered by Inductotherm
Group
company
Inductotherm
Heating & Welding Ltd of the UK, with
commissioning and service support
provided locally by Inductotherm Group
Russia engineers.
With hundreds of Thermatool seam
annealers used to produce API line pipe
and casing products around the world,
Russian producers are assured of no
untempered martensite in the weld HAZ
and optimised weld section Charpy
impact results for demanding material
applications.
The well proven precision automated
carriage positioning system ensures
that all three heat stations can be quickly
adjusted to position the inductors over
the seam of the pipe both laterally and
orbitally to ensure maximum yield and
minimised scrap created after a mill
stop.
Reliably delivered power comes from
industry-leading VIP induction power
supply technology.
Thermatool Variable Inductance
Power (VIP) power supplies provide
optimised matching to thin and heavy
wall.
API pipe and each power supply can
be independently controlled from one
single, central console.
Commissioning is scheduled for early
in 2015.
Inductotherm Heating & Welding Ltd
– UK
Fax: +44 1256 467 224
Email:
info@inductothermhw.comWebsite:
www.inductothermhw.comThe off-line spiral pipe machine on which pipes with
diameters from 508 to 2,235mm will be produced
The entire pipe mill, including the
spiral pipe machine and peripherals,
will extend over a length of 450m
Photo credit: Schuler