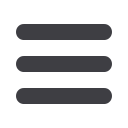

business & market news
18
Tube Products International July 2015
www.read-tpi.com30" pipe to be manufactured in China
Nakata has received its first order for
the newly developed ODF (orbital die
forming) pipe mill from a Chinese pipe
manufacturer. The pipe size is up to
762mm OD, and 25.4mm wall thickness,
and most of the products are API line
pipes up to X80 grade.
Differing from the conventional roll
forming process, ODF is an innovative
technology in which movable dies are
combined to form a continuous tool
surface and work like a huge roll or
moving press machine. This concept
makes the forming process very gentle
and stable, resulting in adaptability to
a wide range of product sizes and
material properties, excellent surface
quality and lower work hardening level
in the material.
Both steel plates and coils can be used as
raw materials in this production line, and
the pipes can be produced in ‘plate-by-
plate’ or ‘coil-by-coil’ style respectively.
This hybrid production process allows
the user to have flexibility in selecting
raw materials corresponding to the size
of lot or dimensions of product. Nakata
has a 4" ODF test machine in its shop,
with which the customer can verify the
performance of the forming process.
Nakata Mfg Co, Ltd
– Japan
sales@nakata-mfg.co.jp www.nakata-mfg.co.jpPolysoude opens its doors in Nantes
Polysoude held open days at its Nantes,
France, headquarters in June. Over the
two days, the company presented its
latest developments in the fields of
welding and weld overlay cladding using
the TIG and TIGer (GTAW) process.
Professionals and decision-makers from
all industries who use welding in their
line of business were invited to come
and discover how they can optimise
their productivity and guarantee a
quality product. Representatives of
the specialised trade press were also
welcome.
Polysoude has always aimed to optimise
its customers’ productivity while
improving the quality of their products
by developing new solutions that tackle
the most complex issues. Workshops
on different topics, described below,
offered opportunities to exchange
information on the various types of
mechanised and orbital TIG/TIGer
welding and cladding applications.
These applications are commonly used
across a wide range of sectors such as
conventional and nuclear power plants,
solar farms, oil exploration, aerospace,
processing of foods and pharmaceutical
products, water treatment, etc.
For orbital welding, it can be easily
demonstrated that using the hot-wire TIG
process with an open head significantly
increases welding speed, and it can
be used to join thicker tubes than the
cold-wire TIG process. Automation via a
program recorded in the power source
guarantees flawless production.
For very thick-walled parts, another way
of increasing productivity in addition to
the hot-wire TIG process consists of
reducing the groove, and therefore the
volume to be filled by the weld. The
use of an open-type carriage welding
head equipped with a narrow gap
torch limits the quantity of metal to be
deposited. Additional gains are made
on preparing the groove by limiting the
loss of material and the machining time.
This technology guarantees a quality
weld thanks to the TIG process and
is perfectly reproducible by virtue of
automation.
When high quality welds are required,
orbital TIG welding is a suitable
technology for tube-to-tube or tube-to-
tubesheet welding applications. With
or without filler wire, this is a stable,
reliable process that can be used on
steel, stainless steel, titanium and nickel
and aluminium alloys, for example. The
development of a welding programme
guarantees a high-quality weld through
automation. The welding cycle can be
repeated as often as necessary with the
same result.
Orbital welding equipment can be used
in difficult conditions such as a confined
space or where there is a lack of
accessibility or visibility. On all of these
machines, the welding parameters can
be checked and compiled into a printable
protocol for guaranteed traceability.
Polysoude
– France
www.polysoude.comA successful start to 2015
Tube Developments has reported a
successful first quarter of 2015, with
the award of contracts around the
world, and the hope of continuing this
success during the rest of the year.
The company supplied process pipes
for the Total Mariner project. The
Mariner is the largest new offshore
field development in the UK in over
a decade, and is located on the East
Shetland Platform of the UK North
Sea, approximately 150km east of the
Shetland Isles. Tube Developments
also supplied structural tubulars to
the Petrobras Iracema Sul project,
where Saipem secured the EPCI
contract.
In January, the company completed
the evaluation procedures for Saudi
Aramco and renewed its vendor
and stockist approval status for the
supply of pipes and tubulars.
Tube Developments Ltd
– UK
info@tubedev.com www.tubedev.com