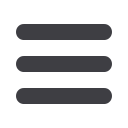

52
Tube Products International July 2015
www.read-tpi.comMater ials handl ing & logist ics
Robot with an elevated payload
A new model has been added to the
Comau range of robots. The Smart NJ
650 features an elevated payload, and
was designed to meet the need for
robots than can efficiently manipulate
components of significant size and
weight.
The robot can handle a payload of up to
650kg, has a maximum horizontal reach
of 2.7m and ISO 9283 repeatability from
0.15mm. Like Comau’s other heavy load
and high reach robots, the Smart NJ
650 is characterised by high stiffness,
a compact, space-saving design and
an optimised load capacity/payload
relationship.
The Smart NJ 650 is suitable for multiple
industrial applications, including
handling, spot welding of large body
parts for the automotive sector, and
the manipulation of heavy components
for machine tending operations, as well
as palletising, deburring and polishing,
packaging and machining in general.
It can also be deployed within the
food and beverage industry, foundry
operations or virtually any other
industrial sector.
Arturo Baroncelli, segments manage-
ment director at Comau, said, “The
new Smart NJ 650 allows us to expand
and strengthen our presence in market
segments that need to process heavy
pieces. It also enables us to respond to
new production areas that increasingly
require robots with a large payload
capacity.”
Comau SpA manufactures flexible,
automatic systems and integrating
products, processes and services that
increase efficiency. Headquartered in
Turin, Italy, with an international network
that spans 15 countries, Comau
offers systems, welding lines and
body assembly lines (body welding),
machining systems for the assembly of
engines (powertrain), and a wide range
of industrial robots for all application
areas. The company also provides eco-
sustainability and maintenance services
for a wide range of industries.
Comau SpA
– Italy
www.comau.comThe new Smart NJ 650 has a load capacity
of 650kg and reach of 2.7m
Tubular handling systems
Essentra Pipe Protection Technologies
in Aberdeen, UK, was established in
1965 to service the North Sea oil and gas
industry. Within its 5,000ft
2
production
facility, equipped with CNC lathes and
polyurethane casting machinery, the
company is able to provide a wide range
of premium, API tubular and drill pipe
thread protectors, special protection
products, stabbing guides and tubular
handling systems.
The company’s Rhino
®
tubular handling
system is designed to provide a safe,
efficient and easy-to-use method of
transportation for tubular products,
worldwide. The Rhino exceeds existing
pipe handling specifications, ensuring
maximum safety for handling crew, the
transporter, and the general public. It
can be modified to accommodate any
combination of tubular goods, including
accessories fitted to the pipe prior
to transit. It also increases shipping
flexibility to accommodate a variety of
pipe sizes.
The system eliminates metal-to-metal
contact, and allows high-density
stacking. Lifting eyes facilitate any
type of handling or loading, including
truck, rail, ship and offshore transport.
Premium materials and construction are
employed to ensure years of service.
The system is designed to lift and
handle loads with a large safety margin,
providing unlimited storage options and
maximum storage room. A variety of
pipe sizes are accommodated, and the
system is manufactured to meet 6 or 12
metric ton lifting capacity.
Essentra Pipe Protection Technologies
– UK
www.essentrapipeprotection.comPipe protection
technology