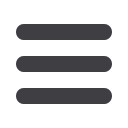

Industry News
www.read-tpt.com24
J
anuary
2016
Testing systems for
ERW-welded pipes
TWO ultrasonic testing systems for
ERW-welded pipes were to be installed
at the Polish pipe mill Huta Labedy in
2015. They are part of a completely new
pipe mill, realised by the SMS Group
fromMoenchengladbach, Germany. The
SMS Group was also the contractual
partner of Karl Deutsch.
Basis of the contract were pipes with
following dimensions: diameters from
114mm to 324mm, wall thicknesses
from 3mm to 16mm and lengths from
6m to 18m. After forming the steel strips
and welding, a first ultrasonic testing of
the longitudinal weld is performed on
the (still) endless pipe. The ultrasonic
probes are mounted on a carriage,
which is mounted to a machine stand.
The carriage is placed on the top of the
pipe and follows the pipe with rollers in
an optimal way.
The carriage can be into a service
position (offline) to check the calibration
on a short reference pipe. The reference
pipe can be moved motor-driven,
allowing a dynamic verification of the
calibration.
The carriage contains five probes,
all working with a water delay line for
ultrasound coupling. Four probes are
used for longitudinal flaw detection, two
of them for inner flaws and two for outer
flaws. The fifth probe is an oscillating
straight
beam
probe,
measuring the wall thickness
in the area of the weld seam
and controlling the quality of
the scarfing.
At the end of the production
line, the pipes undergo final
testing executed by means
of a testing bridge since this
concept provides maximum throughput.
In the extreme case 140 pipes per hour
have to be inspected.
The self-supporting bridge, with an
overall length of 30m, is equipped
with probe carriages on both sides. In
twelve o’clock position the longitudinal
weld seams are inspected first. Then
the pipes are transported transversally
underneath the bridge into the second
testing position. Here, the pipes are
rotated and tested for delaminations on
the full pipe body. Both testing positions
are equipped with calibration units,
which allow a reproducible calibration
of the probes’ sensitivity with the aid
of short tube sections (left side in the
picture above).
The weld testing is performed by a
total of eight probes mounted on a single
carriage, working with a test speed of
2m/s. As in the first testing system, four
probes are used for longitudinal flaw
detection.
The remaining four probes are used
to inspect the heat-affected zone next
to the weld for delaminations. The
rotational inspection of the pipe body is
carried out at a circumferential speed of
approximately 1.5m/s with five special
TR-probes with three channels each.
Each probe has one transmitter and
three receiver channels, yielding a scan
width of 50mm.
The total scan width of 250mm from all
five probes enables a high throughput.
Ultrasonic coupling is performed by a
water gap and all probes are mounted
in holders, which perfectly follow the
surface even in case of changing radius
curvatures.
Additionally, the probe holders are
designed to cover the entire diameter
range without the need for mechanical
changes.
Karl Deutsch GmbH
– Germany
Website:
www.karldeutsch.deArrangement of probes for weld inspection on the endless
pipe
Fives to supply a new vertical
furnace to South Korea
POSCO, an autosheet manufacturer,
has entrusted Fives with a contract for
design and supply of a high-performance
vertical annealing furnace for the new
hot-dip galvanising line at POSCO’s
Gwangyang plant in South Korea.
In line to expand its production of
premium automotive steel sheet for
global carmakers, POSCO launched the
construction of its seventh continuous
galvanising line (CGL) at its largest
and most modern plant of Gwangyang
Steelworks on Korea’s southern coast.
CGL No7, a specialised production
line with an annual production capacity
of 500,000 tons dedicated to the high-
end GI/GA exposed and advanced high
strength steels (AHSS), is expected to
be completed in 2017.
The vertical annealing furnace is
critical process equipment needed to
produce the latest AHSS grades, which
are becoming an important part of
steelmakers’ strategy. Fives will design
and supply its latest generation Stein
Digiflex
®
vertical annealing furnace,
including the patented Flash Cooling
®
technology operating at high H
2
rate
(up to 65 per cent H
2
) and the latest
AdvanTek
®
2.0 radiant tube combustion
system operating with coke-oven gas.
Fives stated that it gained the contract
by offering the best operational
expense savings, production flexibility,
accuracy of operation and compact
furnace design. The last two continuous
galvanising
lines
of
POSCO’s
Gwangyang plant, CGL No5 and CGL
No6 producing exposed panels and
HSS grades, are also equipped with
Fives vertical annealing furnaces.
Fives Group
– Russia
Fax: +7 495 775 48 40
Website:
www.fivesgroup.com