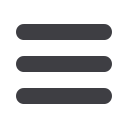

58
Wire & Cable ASIA – November/December 2016
www.read-wca.comGiven the specific application environment, the flat
cable was designed with an outer sheath, sub-unit
sheath, tight buffered fibre, FRP and strength member.
See
Picture 1
.
3.2 Different combinations of materials of the flat cable
The flat cable was a tight-structure cable, but after
stripping 20-30cm of the outer sheath, the sub-unit cable
could not adhere to the outer sheath.
Moreover, the flat cable must meet the requirements of
flame retardancy. Therefore, the outer sheath and sub-unit
materials both have the flame retardant property and high
temperature resistance property.
Taking the users’ actual needs and the application
environment of the cable into consideration, three different
combinations of materials of the flat cable were designed
to verify the processing performance and the overall
performance of the cable.
That is, three different combinations of sub-unit material
and outer sheath material. The first combination was HDPE
(high-density polyethylene) outer sheath material and PVC
(polyvinyl chloride) sub-unit material.
The second combination was LSZH (low smoke zero
halogen) outer sheath material and PVC sub-unit material.
And the last combination was LSZH outer sheath material
and LSZH sub-unit material.
After the cable structure was set, the mould was designed
according to the materials behaviour and the processing
parameters adjusted continually to settle various problems
that appeared during the cable processing.
This then underwent repeated processing verification,
and it was found that the first and the second designs of
the cable could satisfy the stripping requirements. That
is to say, the flat cable with HDPE outer sheath and PVC
sub-unit, or with LSZH outer sheath and PVC sub-unit
could both assure that the sub-unit cable did not adhere
to the outer sheath after 20-30cm of the outer sheath
was stripped.
For the last design, the LSZH outer sheath materials and
the LSZH sub-unit materials easily adhered to each other.
Although this could produce a small amount of sample
to meet the stripping requirements, the continuity and
consistency of processing for the cable could not be
guaranteed, so it was not recommended to adopt this
structure.
4 Main properties of flat cable
4.1 Performance requirements
All specifications of the flat cable are determined by the
installation and the usage of the cable.
Table 1
below shows an overview of the requirements
of the cable. After the continuity and consistency of
processing for the flat cable, severe measurement to the
properties of the two qualified cables according to
Table 1
were conducted.
In the following sections, all the tests and results are
described.
4.2 Test results
4.2.1 Transmission property
The transmission property of the cable was measured by
an OTDR (optical time domain reflectometer) according to
IEC 60793-1-40.
Test
Specified value
Acceptance criteria (1,550nm)
Attenuation of cable
IEC 60793-1-40
1,310nm
1,550nm
α
≤0.4dB/km
α
≤0.3dB/km
Tensile
IES 60794-1-2-E1
1,350N for 1 min
∆
α
≤0.1dB/km,
fibre strain≤0.6%,
No damage to
cable outer sheath
Crush according to
IEC 60794-1-2 E3
500N/10cm for 1 min
∆
α
≤0.1dB/km,
No damage to
cable outer sheath
Water penetration
IEC 60794-1-22 F5
3m sample, 1m depth of water for 24h
No penetration
Temperature cycling
IEC 60794-1-22 F1
-20˚C/+60ºC,
two cycles
∆
α
≤0.1dB
Vertical flame propagation for single
sample
IEC 60332-1-2
600mm sub-unit sample, 60s flame
application
The distance between the lower edge
of the top support and the onset of
charring is greater than 50mm
❍
❍
Table 1
:
Overview of requirements of the flat cable
Outer sheath
Sub-unit sheath
Tight buffered fibre
FRP
Strength member
❍
❍
Picture 1
:
The cross section of the flat cable