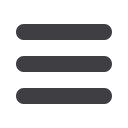

J
uly
2011
131
›
A
rticle
Shandong Province Sifang
Technical Development Co Ltd
– China
Fax: +86 531 88876693
Email:
sdsf@vip.163.comWebsite:
www.cnsdsf.comhigh chromium alloy casting rolls have advantages in method and
cost of manufacture. The effects of saving energy and material are
remarkable through utilising high chromium alloy casting roll.
6. The discussion on development trend
6.1 Casting roll and forging roll
Casting roll and forging roll separately have advantages and
disadvantages. For special-shaped roll, which have the features of
complex shape, more sizes, small batch, the casting high chromium
alloy roll process have notable results for saving energy and saving
raw material. Certainly the high chromium alloy-casting roll is still to
require further perfection.
6.2 Centrifugal casting method and conventional casting
method
The roll with centrifugal casting method has a lot of advantages
over the roll with convention casting method in the qualities. After
the 1990s the roll with centrifugal casting method had a bigger
development used in plate and strip steel production at home, but
it is difficult to popularise in the production of welding pipe roll. The
main cause is that the structure and shape are different between
roll used in welding pipe production and roll used in plate and strip
steel production, one piece of drawing of welding pipe roll is only to
produce one or two pieces, so it is not economic to do a centrifugal
casting mould. If utilising conventional casting methods it is too
difficult to do high chromium alloy casting and is easy to produce
a defect. If utilising a centrifugal casting method it is requested to
utilise special centrifugal casting methods. If utilising conventional
casting methods a series of technical methods must be used to
ensure quality of casting piece.
6.3 Bimetal complex method and single metal method
Whether utilising a bimetal complex method or single metal method
it is important to think about the shape, working condition and the
working layer thickness of rolls. The aim of utilising bimetal complex
method is to save the noble metal and to increase the whole
strength and toughness of the roll, this is as a principle.
The bimetal complex method also has many ways that are better to
accord with the production requirement of steel pipe roll and cold
forming steel roll, but which need further research and practice.
The options are as follows:
(1) The metallurgical combining option: the centrifugal and non-
centrifugal complex casting. At the present a lot of roll for
steel plate and steel strip are produced by centrifugal complex
casting. Now this technology has been perfected day by day,
but the material for working layer is gradually developed towards
high alloying, high wear resistance and so on.
(2) Inlay complex casting option: the way has also got success
under the condition of lower load.
(3) Machine combining option: now the most of straightening roll
for steel pipe has been changed from whole forging structure
of roll and axle to dividing structure of roll sleeve and axle.
Through interference fit and differential temperature mounting
the application result is better. The roll for PQF steel pipe mill is
also changed from whole body structure to dividing structure of
roll sleeve and axle, and the result is successful.
(4) Surface engineering option: the ways included plating, seeping,
spraying, coating and so on are used in difference piece and
the result is successful, the surface layer is too thin so the
application limit is restricted.
References
[1]
Yang Xiuqin ‘Actuality, Problems and Developing Foreground
of China’s Steel Pipe Industry’ Xi An: colloquia for third annual
meeting of 5
th
session of pipe science committee steel rolling
academy of China metallurgy academy.
[2]
Fu Hanguang, Xing Jiandong ‘High Speed Steel Roll Manufacture
Technique’ Beijing: metallurgy industry publishing house. 2007.6
[3]
Lin Huiguo ‘Pocket World Steel Grade Manual’ Beijing:
mechanical industry publishing house 2003.6
[4]
Chen Huahui, Xing Jiandong, Li Wei ‘Wear Resistance Material
Applying Manual’ Beijing: mechanical industry publishing house
2006.8
[5]
Association of iron and steel engineers ‘The Making, Shaping
and Treating of Steel’ Printed in USA by Herbick & Held
Pittsburgh, Pennsylvania, 1985
[6]
Li Jionghui, Lin Decheng ‘Metallograph of Metal Material’
Beijing: mechanical industry publishing house 2006.6